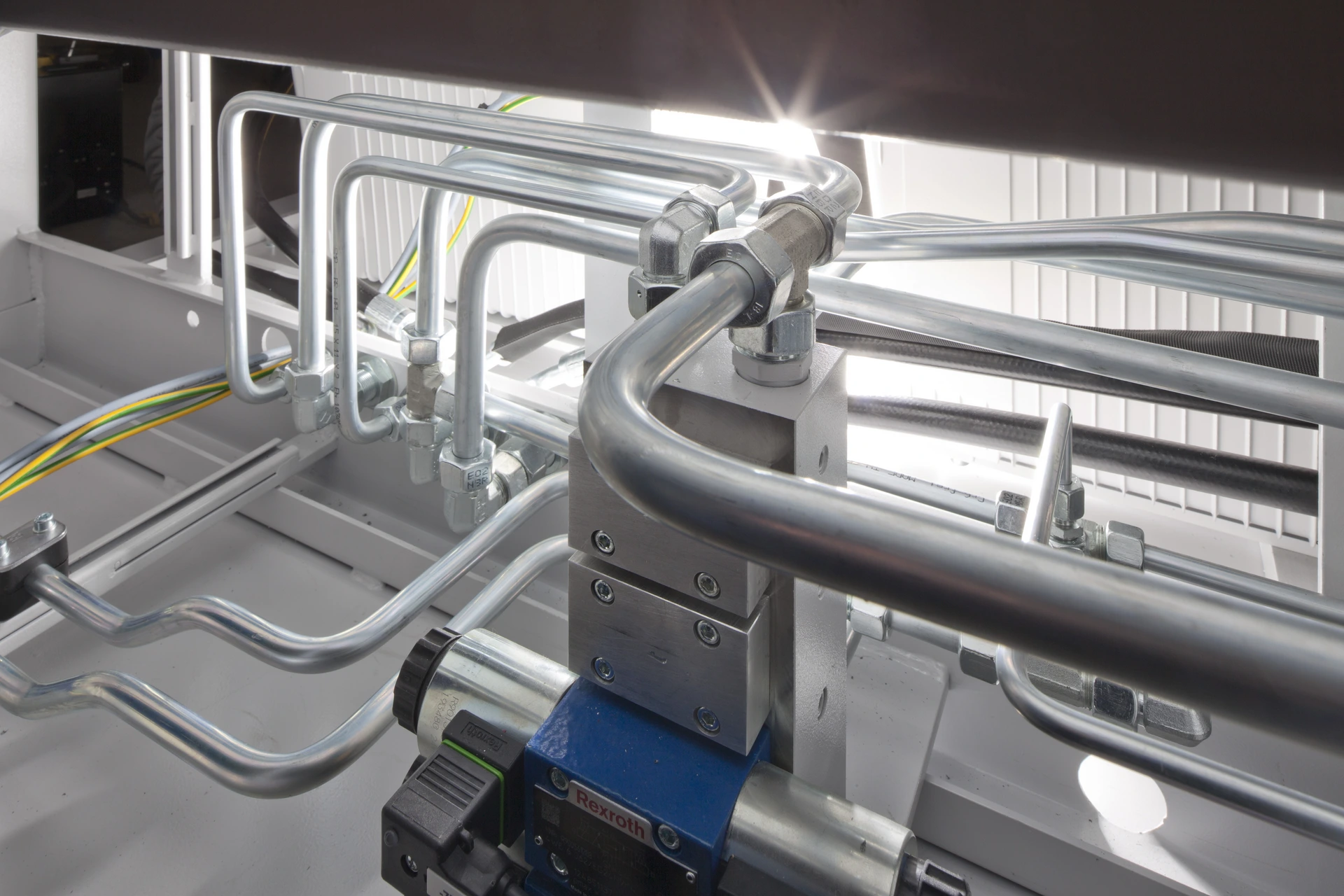
Fast and safe: t work ASSEMBLY DEVICES
GREAT FLEXIBILITI AND IMPRESS WITH THEIR PERFORMANCE
Catalog Download
transfluid® offers the complete package for the production of tubing.
Download our new catalogue.
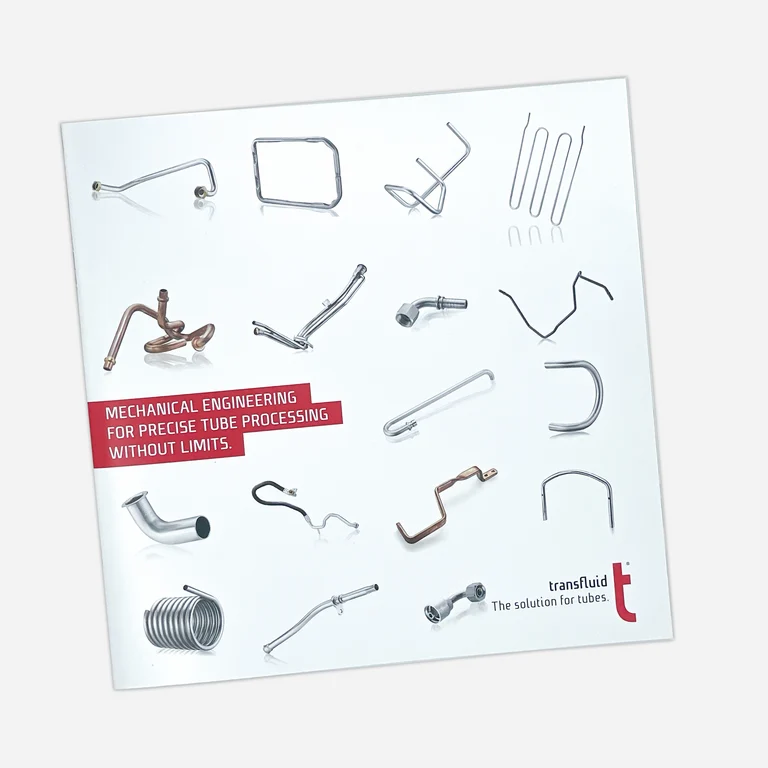
GREAT FLEXIBILITI AND IMPRESS WITH THEIR PERFORMANCE
Catalog Download
transfluid® offers the complete package for the production of tubing.
Download our new catalogue.