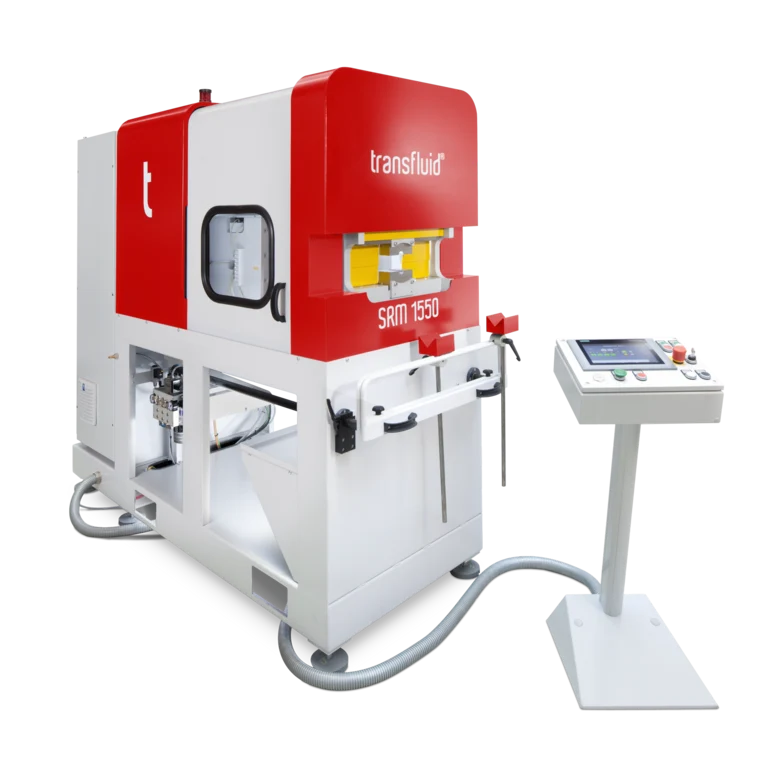
t bend - Type SRM rollforming machines
Our multi tool - All options in one single machine!
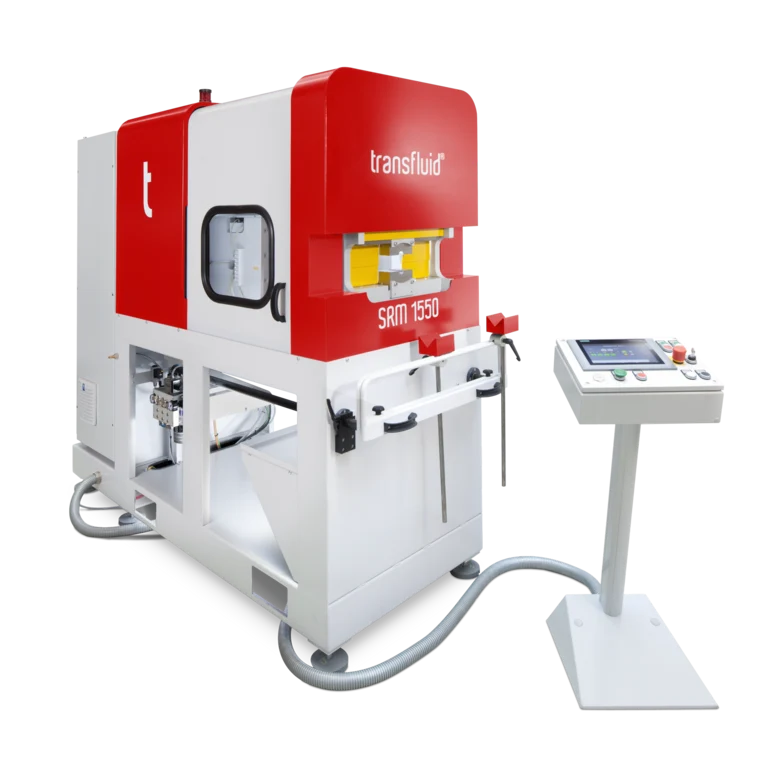
Forming, cutting, post-bending cutting, threading.
For extreme forming degrees with highest precision
Multiple machining steps possible in one cycle
High machining speeds of up to 1500 rpm
Low energy consumption and highest precision due to servo drives
Getting flexible in tube end forming
Ideally suited for the production of challenging contours for sealing elements and for the generation of extremely good surfaces.
The right machine for your task
SRM ROLLFORMING MACHINES
Max. capacity | 4–22 mm |
Wall thickness | 1 mm |
RPM | 300 - 1000 |
Cycle time adjustable | 4 - 10 sec. |
Operation length | max. 40 mm |
Clamping length | 1,0 x D |
Power | 4 kW |
Weight | 1250 kg |
L x W x H | 79 x 35 x 79 mm |
Max. capacity | 5-65 mm |
Wall thickness | 1,5 mm |
RPM | 300 - 1000 |
Cycle time adjustable | 8 - 14 sec. |
Operation length | max. 40 mm |
Clamping length | 1,0 x D |
Power | 8 kW |
Weight | 1700 kg |
L x W x H | 2000 x 900 x 2000 mm |
Max. capacity | 40–127,3 mm |
Wall thickness | 2 mm |
RPM | 50 - 450 |
Cycle time adjustable | 6 - 14 sec. |
Operation length | max. 80 mm |
Clamping length | 1,0 x D |
Power | 8 kW |
Weight | 1700 kg |
L x W x H | 2000 x 900 x 2000 mm |
Max. capacity | 50 - 176 mm |
Wall thickness | 3 mm |
RPM | 80 - 280 |
Cycle time adjustable | 15 - 50 sec. |
Operation length | max. 100 mm |
Clamping length | 1,0 x D |
Power | 12 kW |
Weight | 2200 kg |
L x W x H | 2400 x 900 x 2200 mm |
PREPARED FOR INTEGRATION INTO PRODUCTION CELLS
This series will win you over with its special stability and performance. Individual pieces and small series can be produced in an extremely economical manner with this machine concept. The use of high-value components ensures the machine‘s durability.
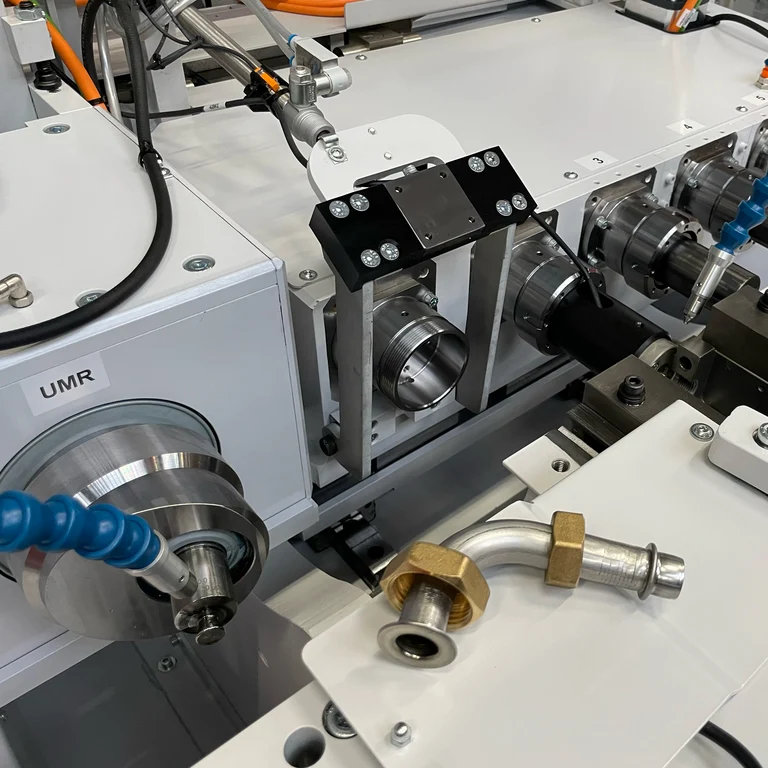
EASY CONTROL VIA TOUCH PANEL
Setting of all parameters centrally in the machine control system, controlled positioning of the forming axis and the stop position.
The UMR is equipped with a completely electronic preselection of the flanging geometry. The stop position and all strokes and machining operations are servo-electrically controlled and can be called up via a touch panel.
Decisive for the exact machining time is which material is used and which shaping is to be implemented. The machine carries out the processing quasi automatically if it is possible to call up the tube size with the necessary process parameters. In individual cases, the clamping lengths for machining are 1 to 1.5 x the pipe diameter.
Our new generation of t form UMR 628, 642 and 2090 machines reduces the set-up time when changing the tools and the operator can set up the machine in less than three minutes.
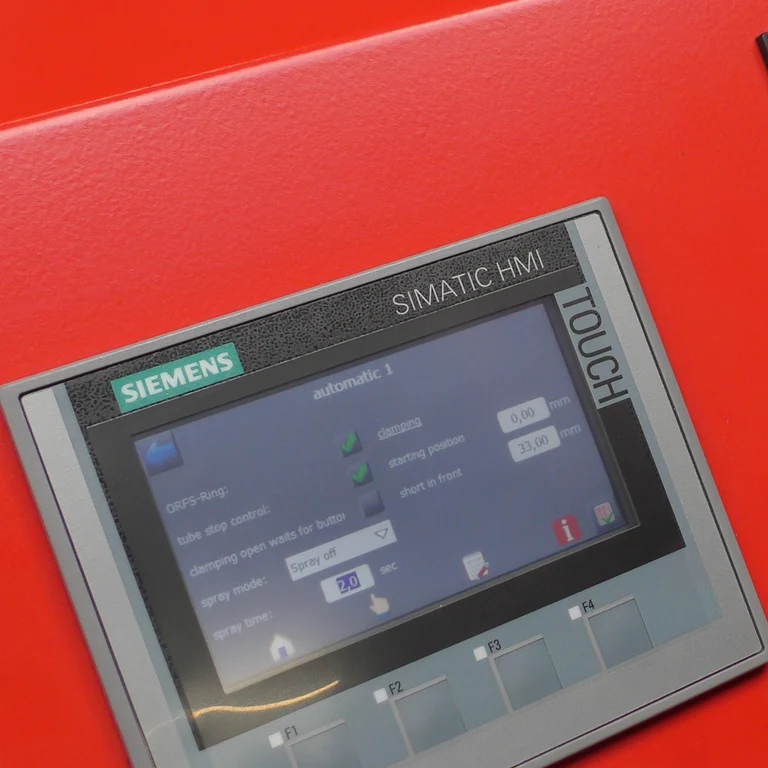
The solution for any geometry with outstanding sealing surfaces
Tailored to your individual requirements and needs, we create optimal solutions with our expertise.
Production samples
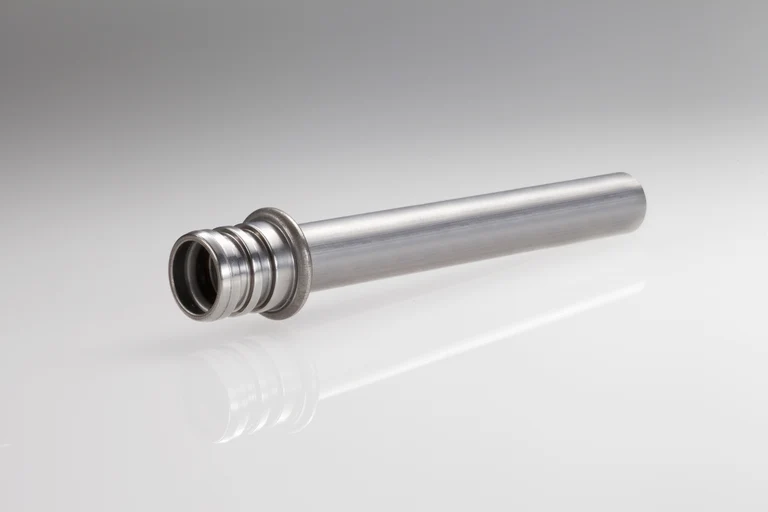
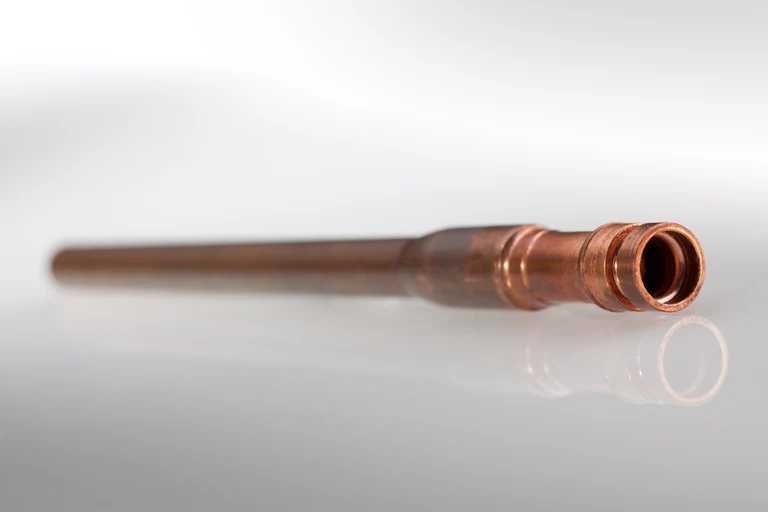
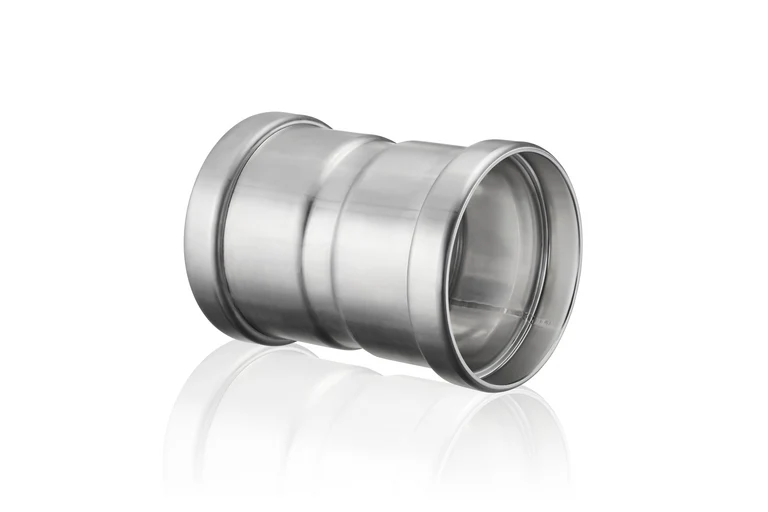
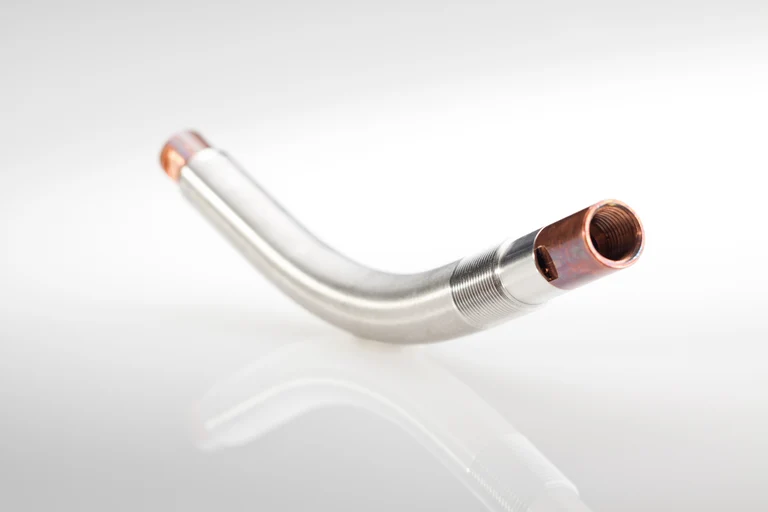
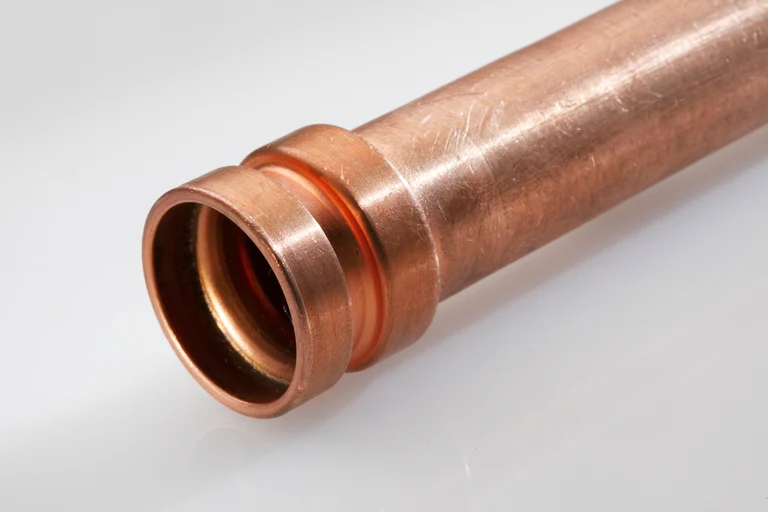
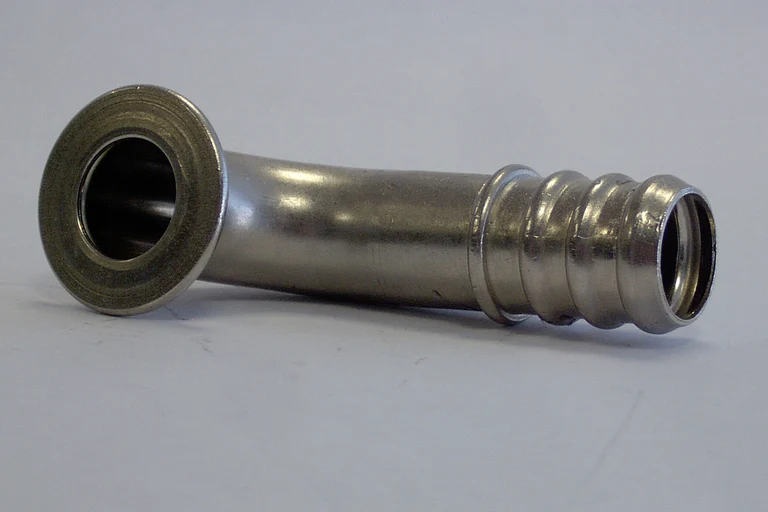
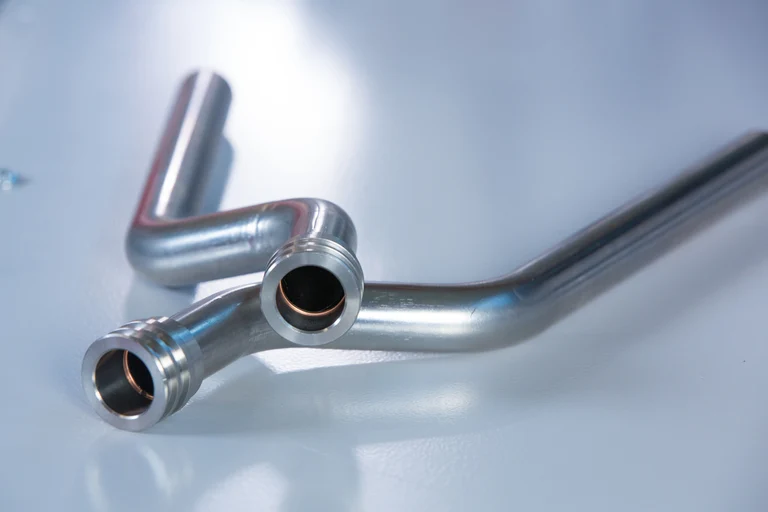
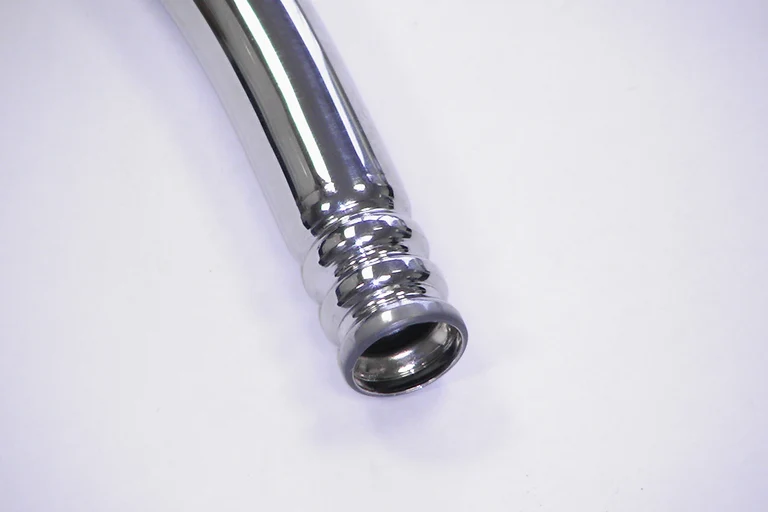
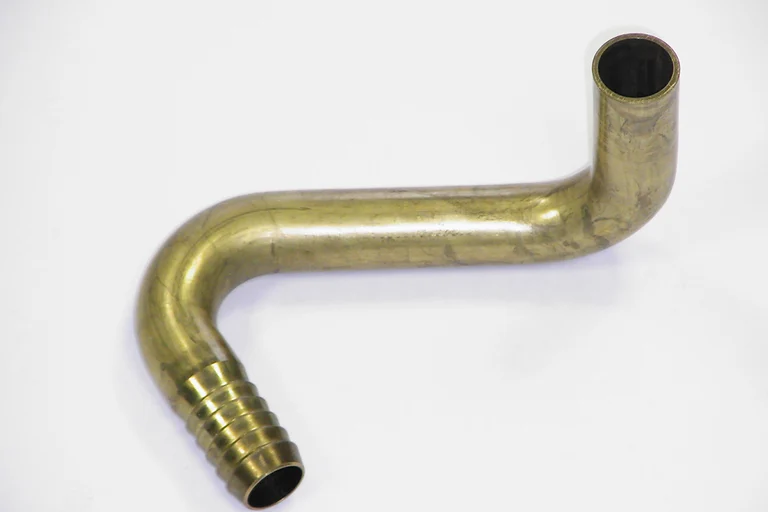
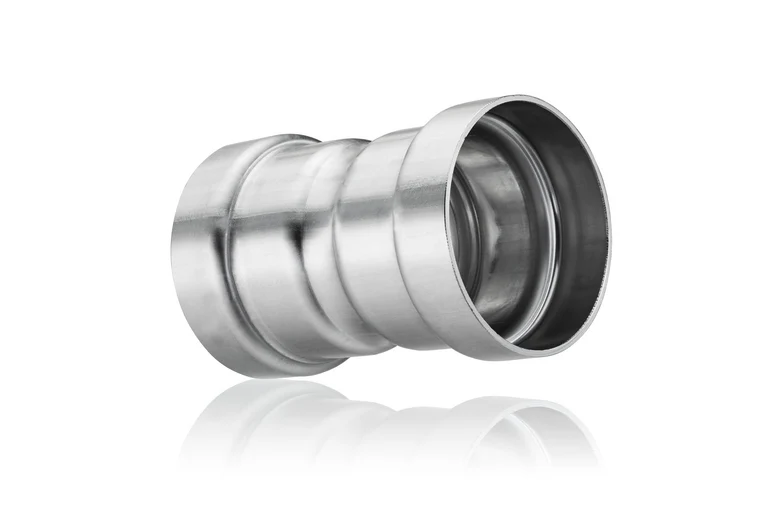
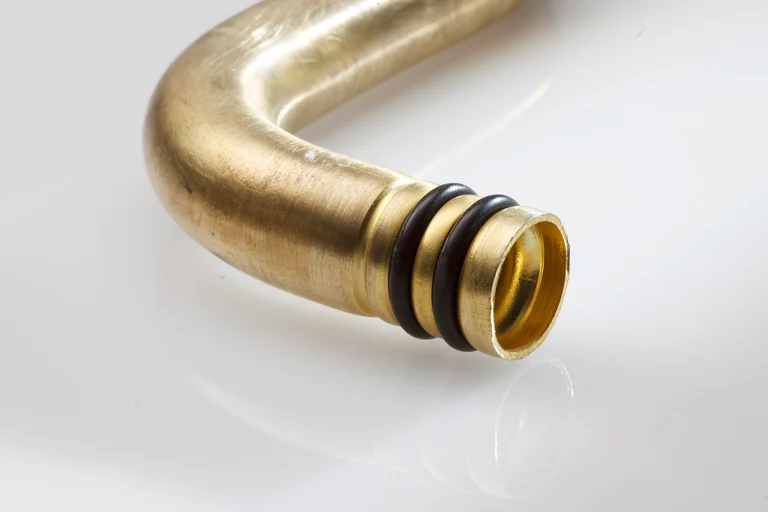
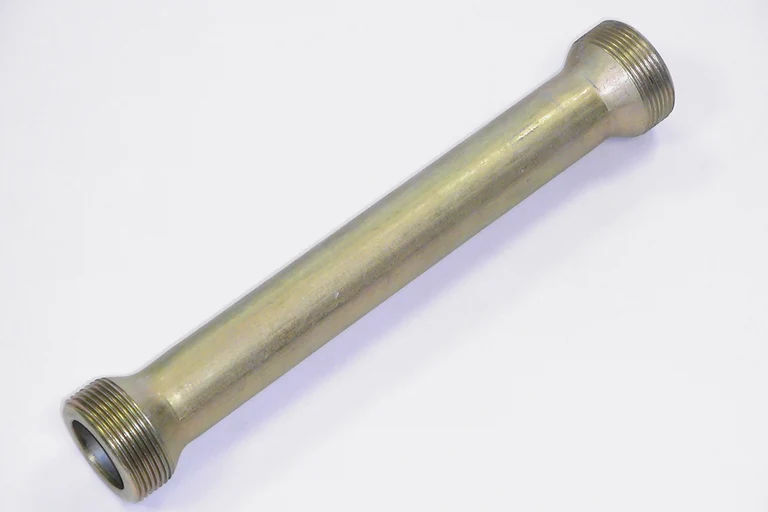
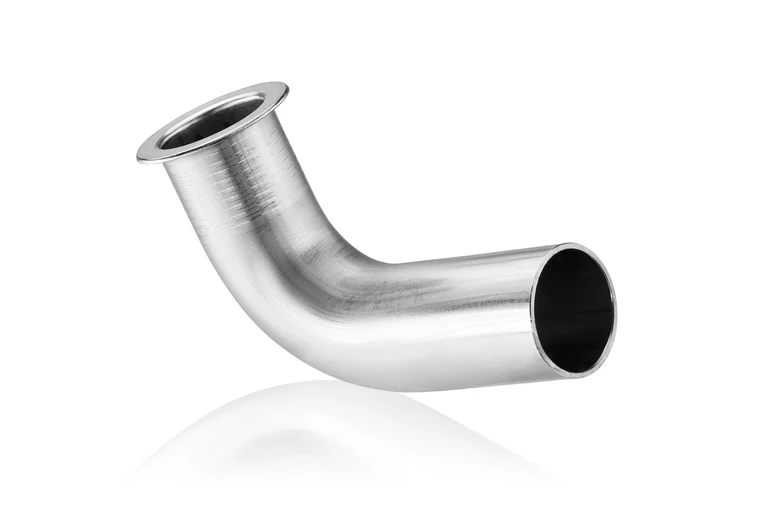
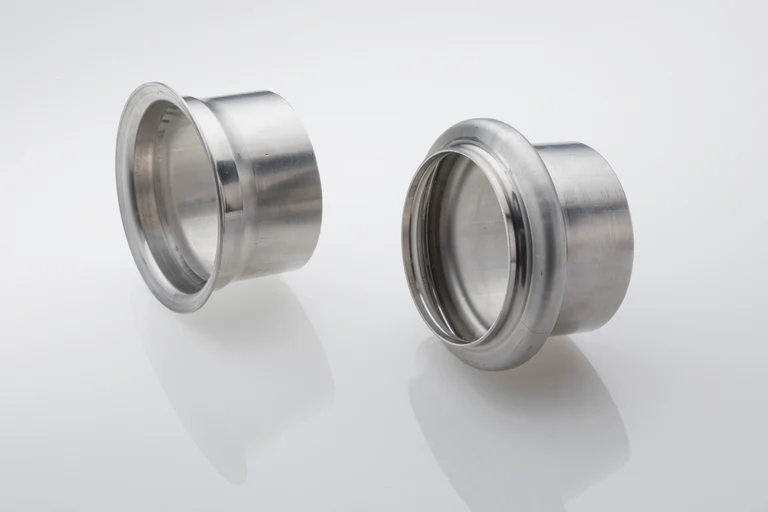
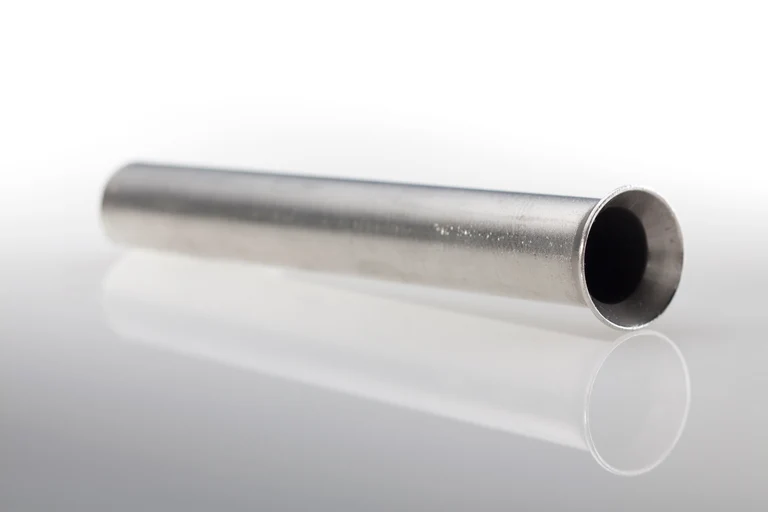
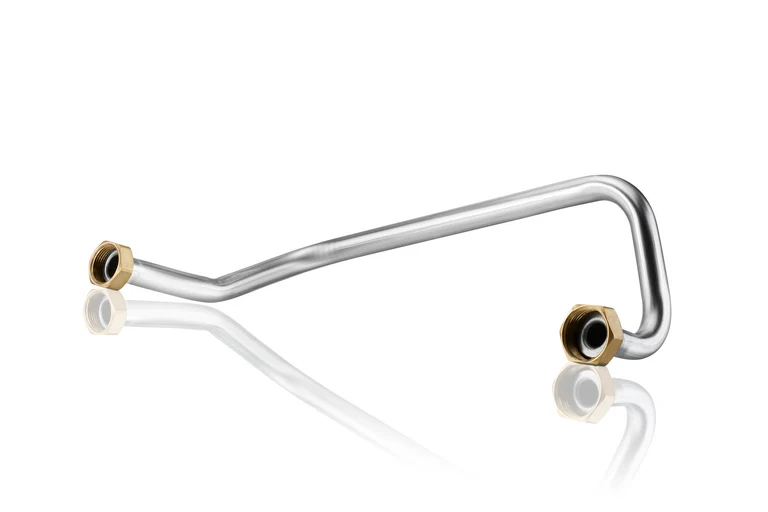
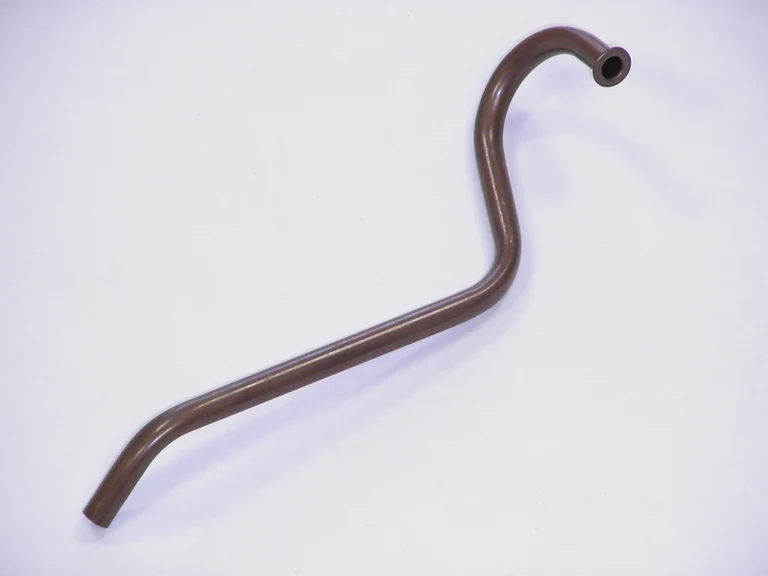
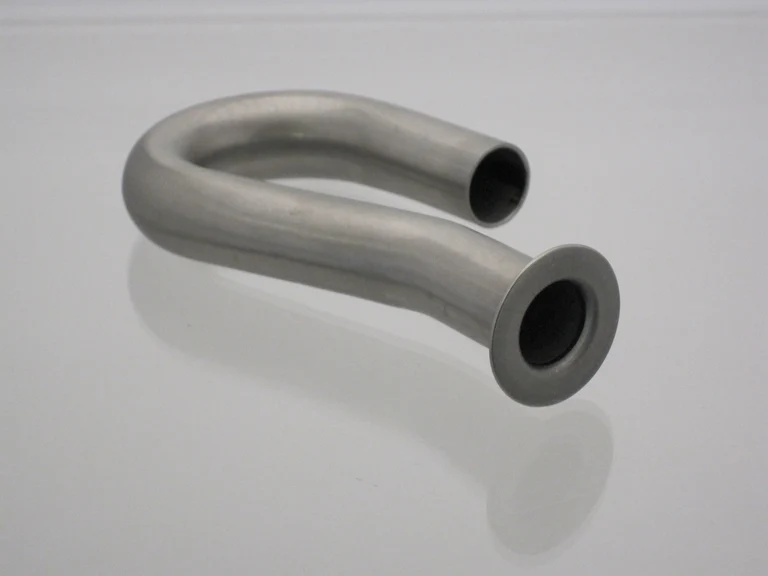
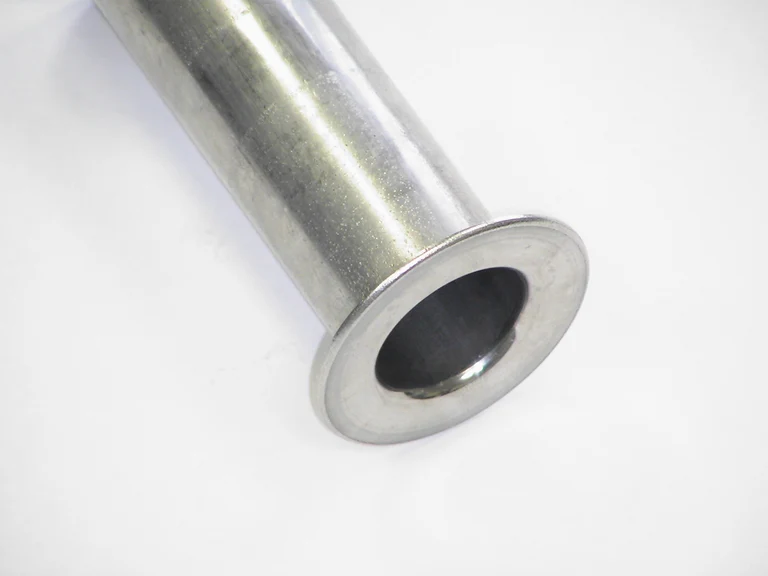
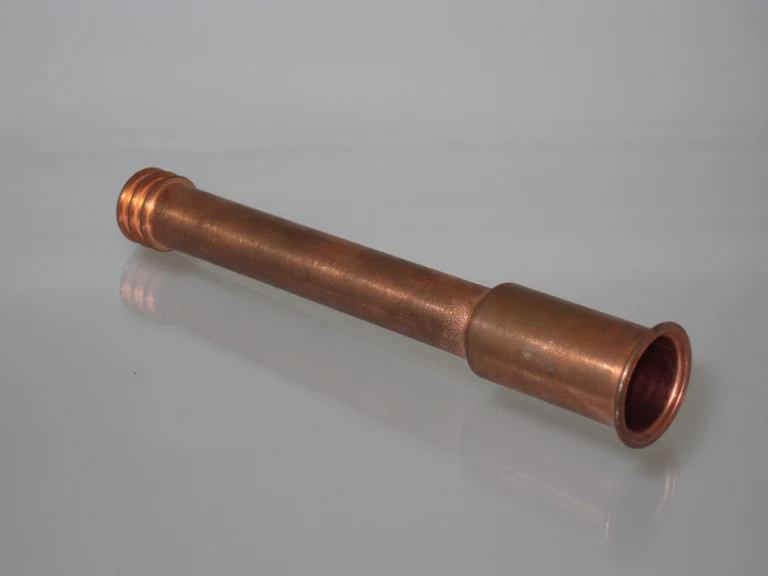
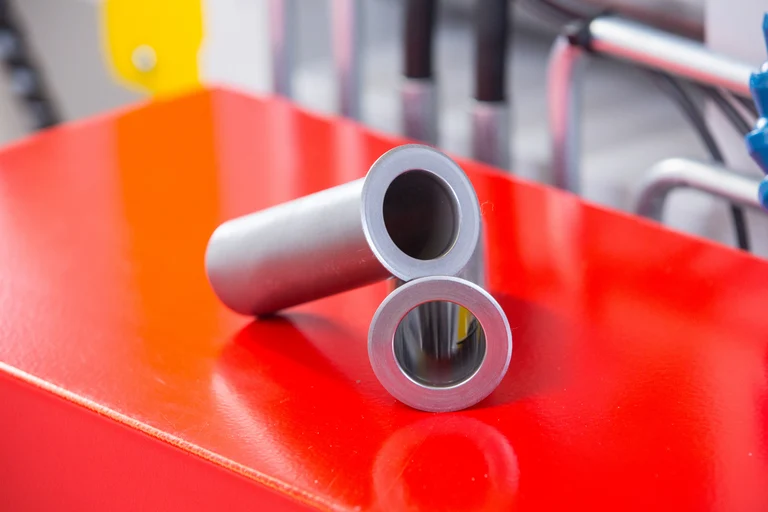
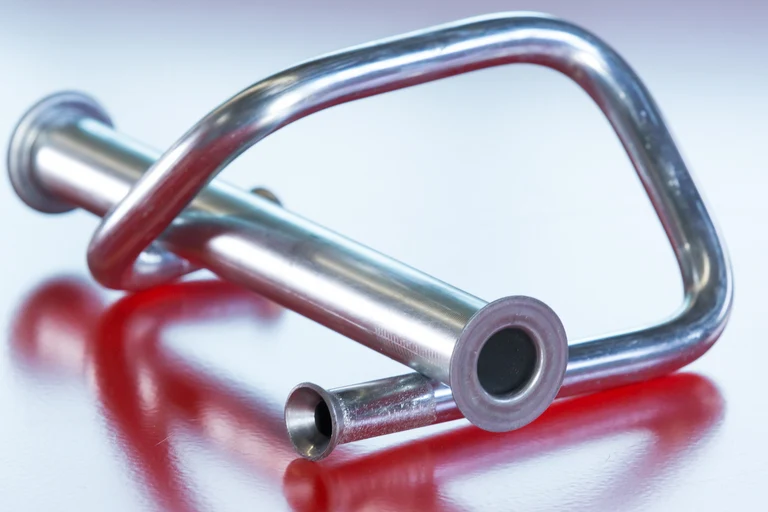
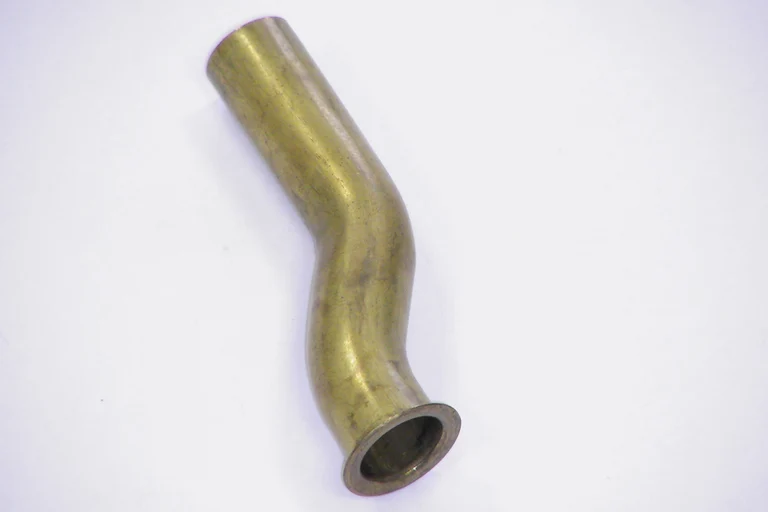
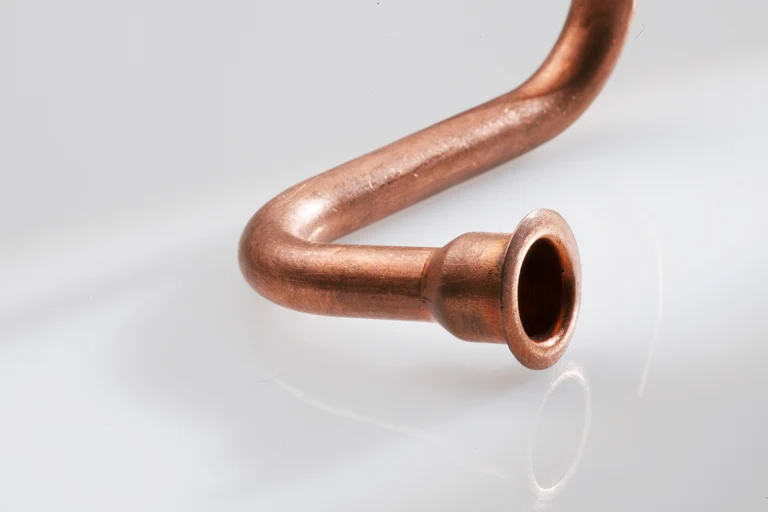
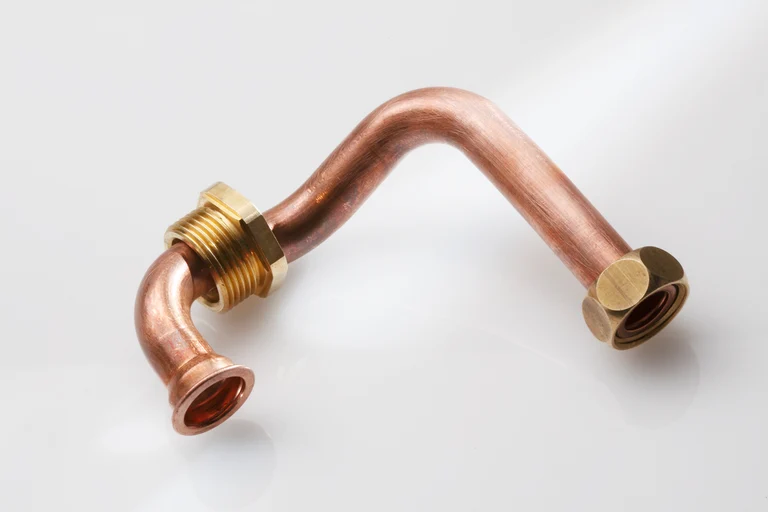
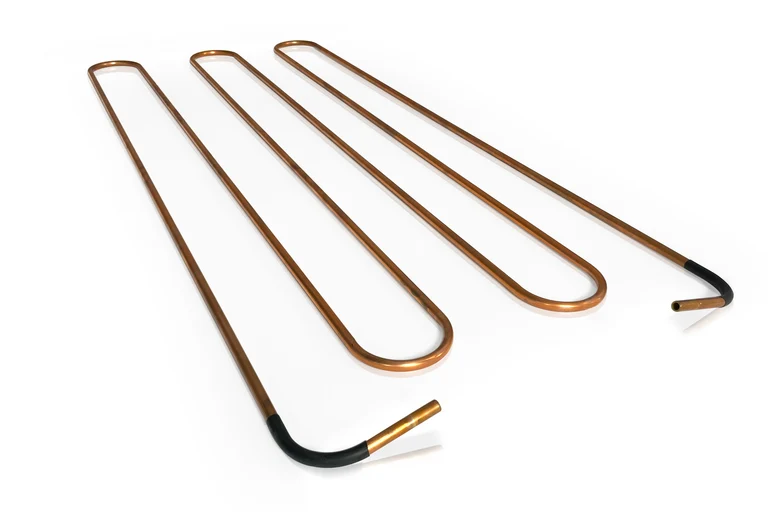
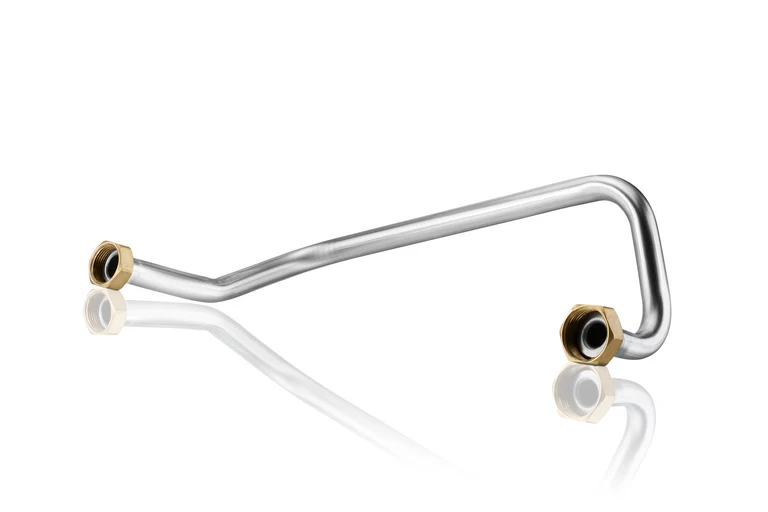
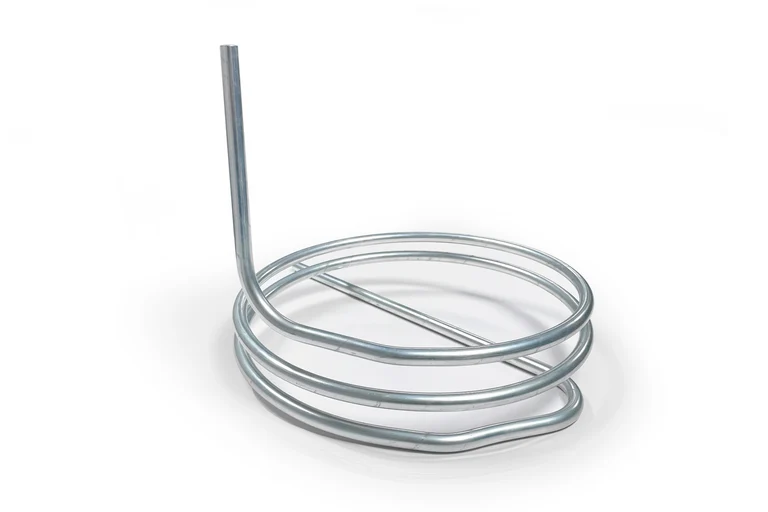
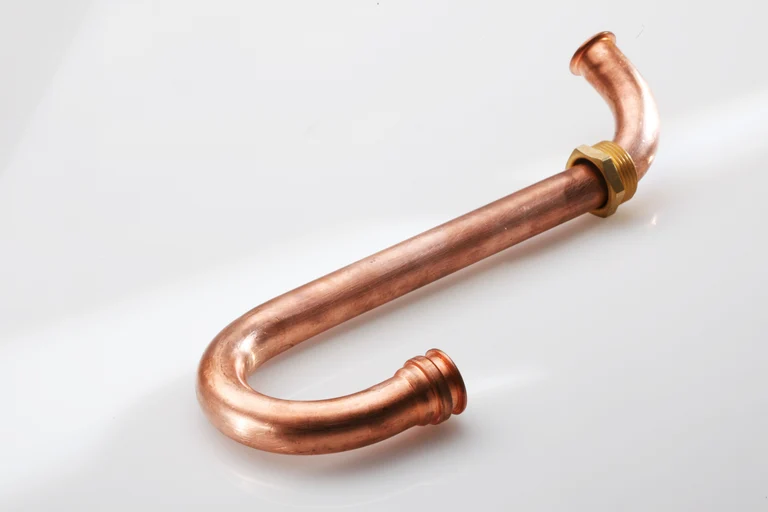
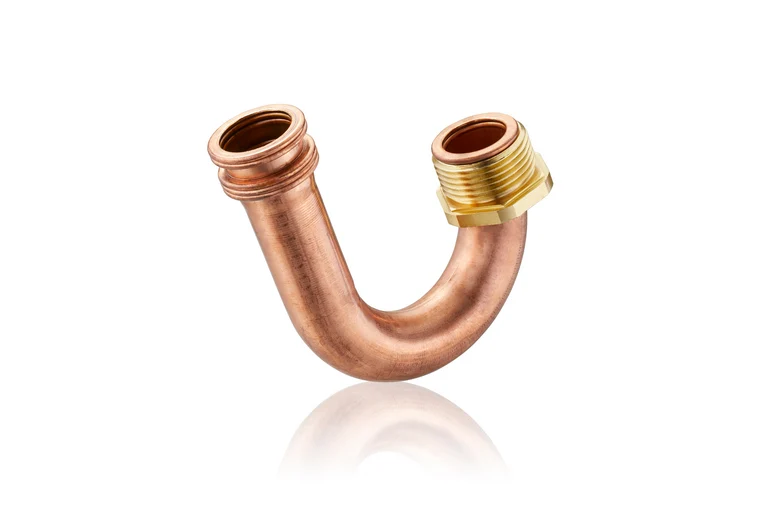
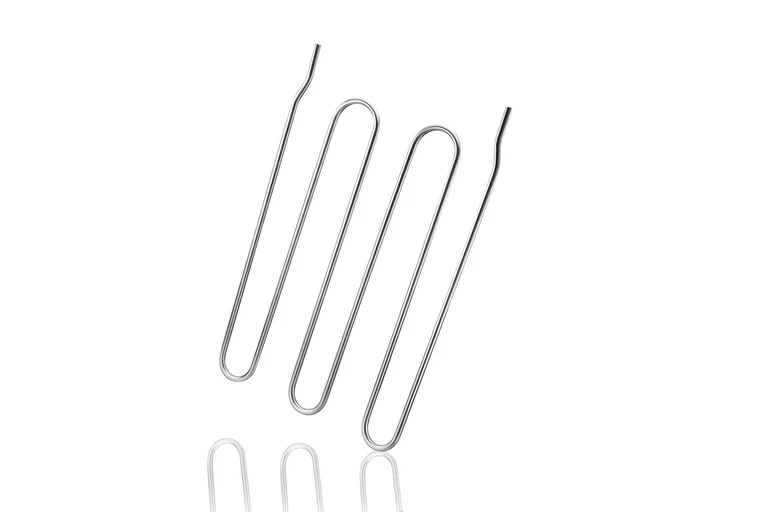
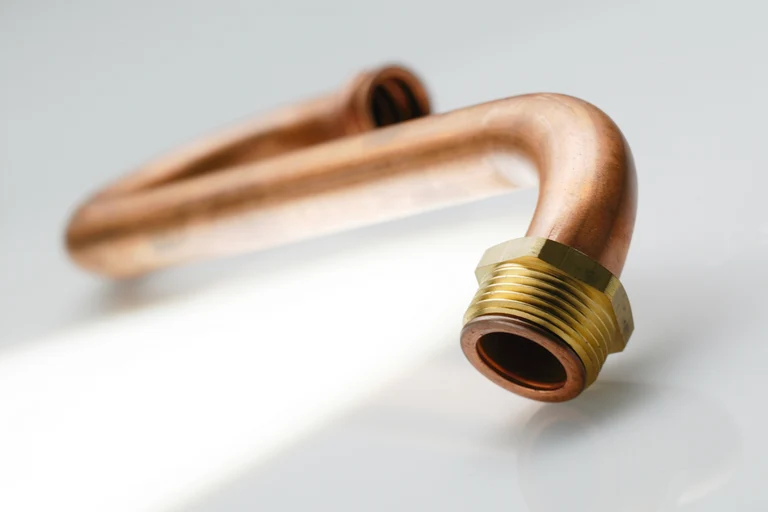
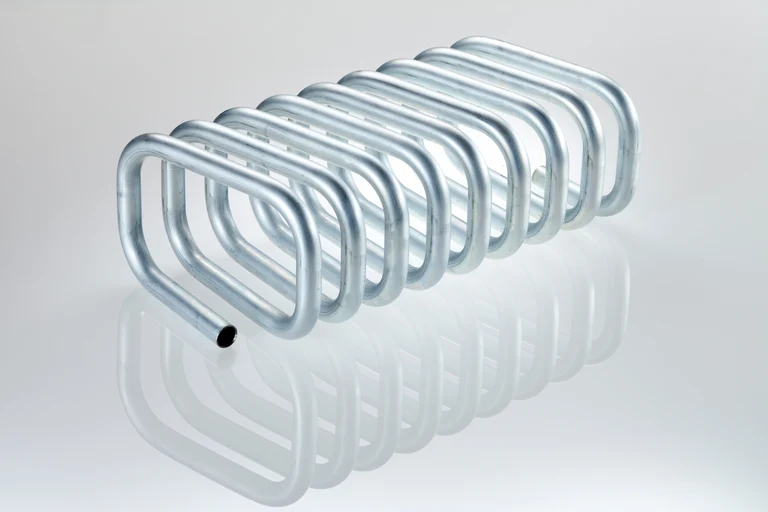
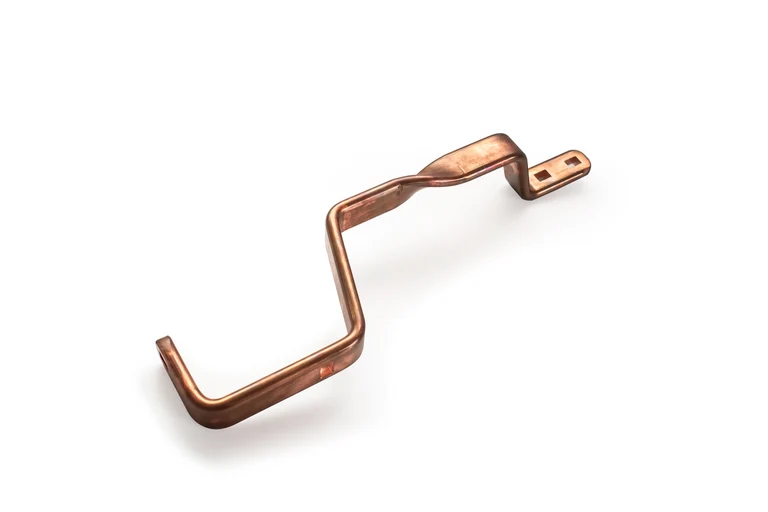
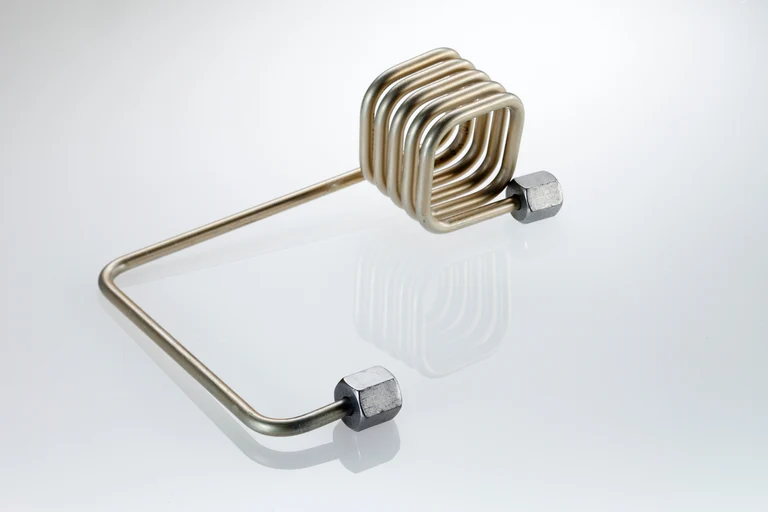
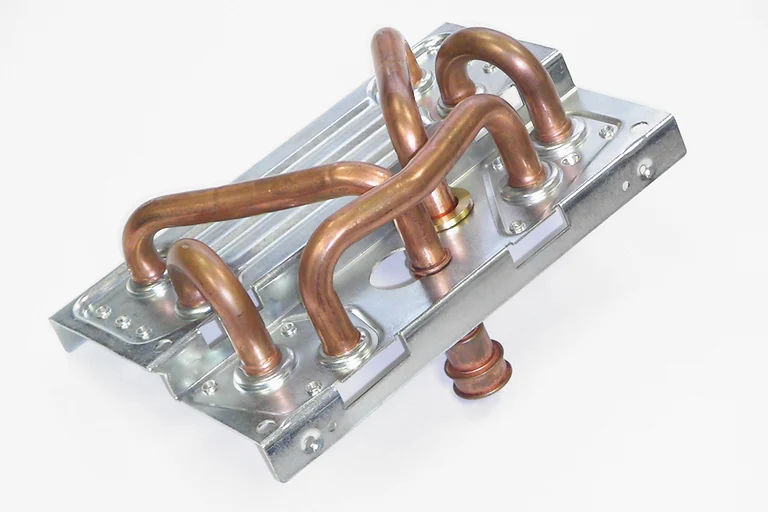
Catalog Download
transfluid® offers the complete package for the production of tubing.
Download our new catalogue.
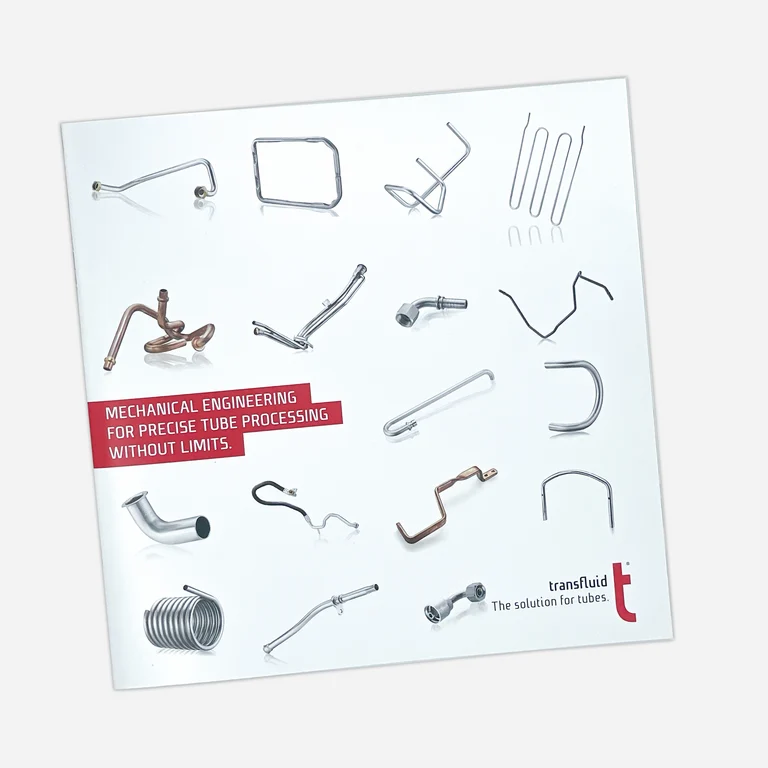