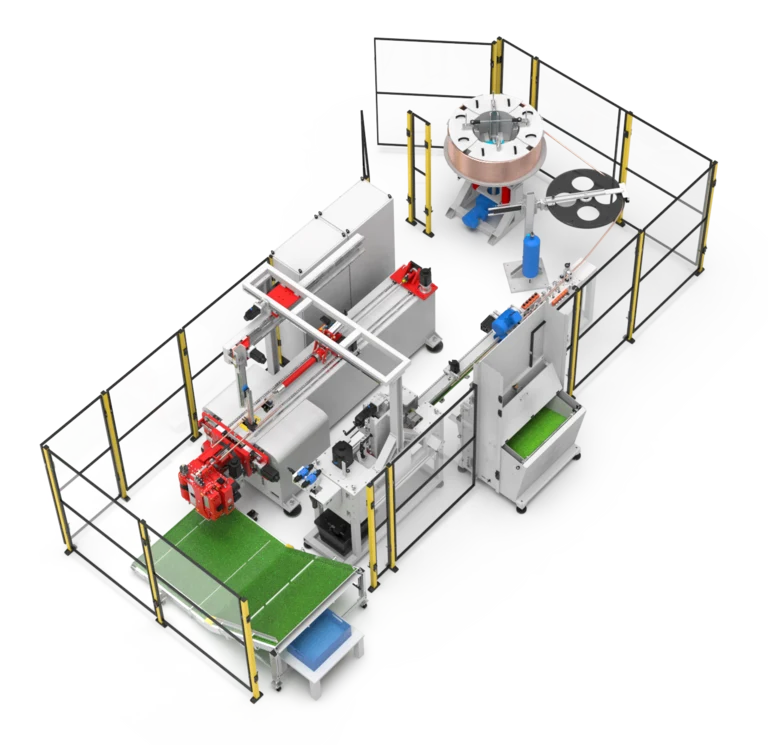
TPC 628: Compact manufacturing cell concept for fully automatic tube production
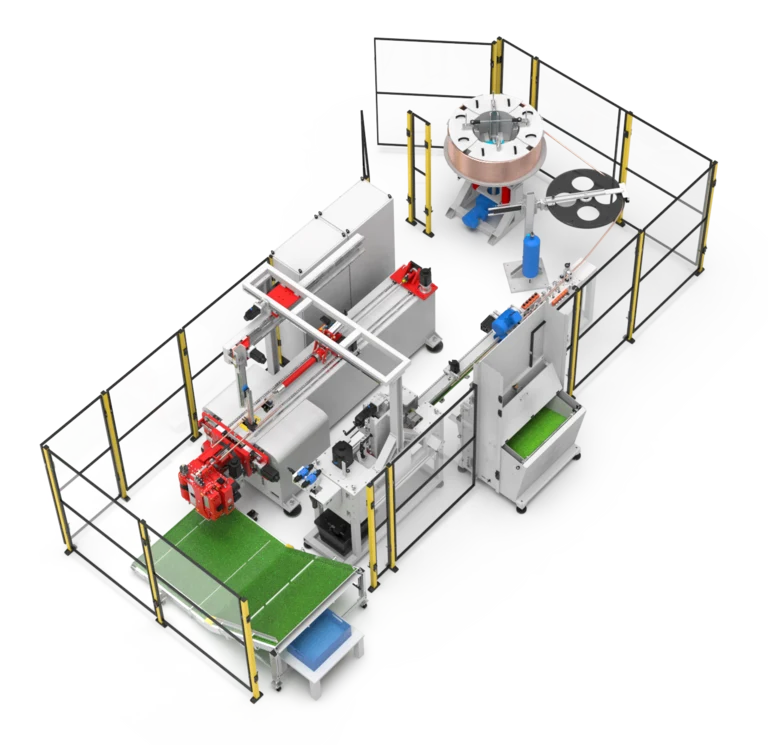
Attractive price/performance ratio
Low space requirement
High flexibility
Adapted solutions for common market requirements
Loading from bar or coil
Processing of tube ends on one or both sides
Copper (up to Ø 28 mm) and stainless steel (up to Ø 22 mm)
Advantages:
- Attractive price, good price / performance ratio
- Extremely compact, small footprint
- High flexibility for short pipelines
- Bending possible with and without mandrel
- Tube ends can be machined on both sides (depending on geometry)
- Arbitrarily expandable
- Punching of holes on the bending machine possible (depending on geometry)
- Volatilizing lubricants that eliminate the need to wash the pipe if necessary
- Low lubricant consumption
- Central plant control
- Fast, easily accessible tool change
- Modular plant design
The right machine for your task
Not sure what you need?
We will find the right machine for your individual requirements. Our team of experts will be happy to advise you.
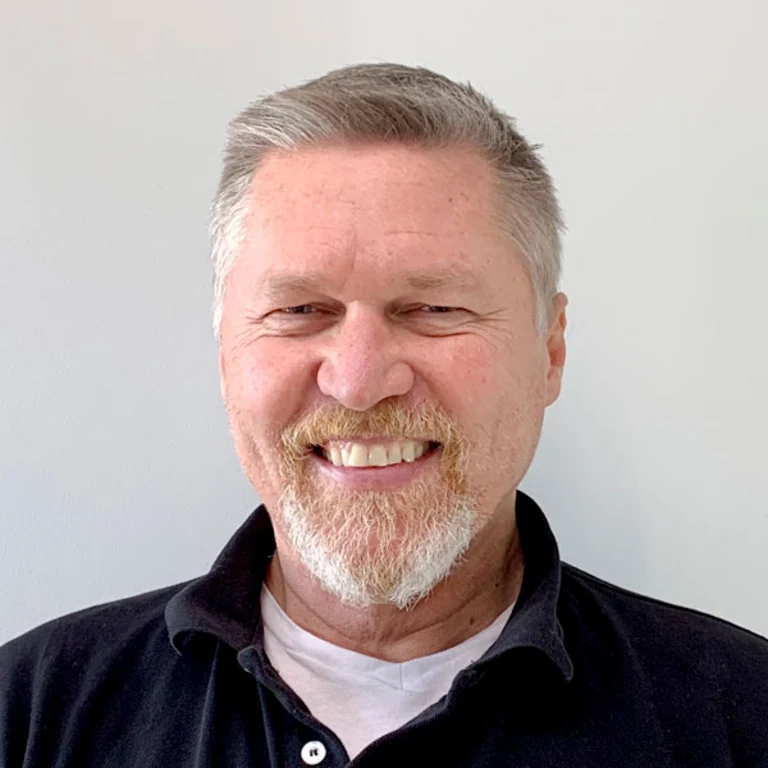