transfluid® t form REB AXIAL FORMING MACHINES
Our solution for complex forming geometries!
Our type REB axial forming machines, with their compression power of up to 287,000 lbs, are particularly well-suited to effortlessly master complex geometries. With up to 6 forming steps in combination with an additional clamping unit, they will satisfy almost all requirements. The operation is simple and intuitive with a touch panel. The sequence control makes each separate movement of the respective forming step user-friendly and fully programmable.
We offer the option to equip our systems with electric or hydraulic-numerical drives. These forming processes can be completed stepwise in transfer systems to achieve very short cycle times. Simultaneous axis movements ensure fast production processes and an efficient and highly dynamic production.
Getting flexible in tube end forming
Ideally suited for the production of challenging contours for sealing elements and for the generation of extremely good surfaces.
The right machine for your task
REB AXIAL FORMING MACHINES
Max. capacity | 4-20 mm |
Wall thickness | 1,2 mm |
Cycle time stage | 2 - 3 sec. |
Forming length | 60 mm |
Number of forming stages | 3 |
Power | 5 kW |
Weight | 1450 kg |
L x W x H | 1500 x 1500 x 2000 mm |
Max. capacity | 6 - 32 mm |
Wall thickness | 1,5 mm |
Cycle time stage (sec.) | 2,5 - 3,5 Sek. |
Forming length | 80 mm |
Number of forming stages | 3 |
Power | 10 kW |
Weight | 1900 kg |
L x W x H | 1850 x 1600 x 2000 mm |
Max. capacity | 6 - 45 mm |
Wall thickness | 2,5 mm |
Cycle time stage | 3-5 sec. |
Forming length | 90 mm |
Number of forming stages | 3 |
Power | 10 kW |
Weight | 2100 kg |
L x W x H | 1850 x 1800 x 2000 mm |
Max. capacity | 6 - 60 mm |
Wall thickness | 2,5 mm |
Cycle time stage | 3-8 sec. |
Forming length | 180 mm |
Number of forming stages | 3 |
Power | 10 kW |
Weight | 2400 kg |
L x W x H | 2100 x 1800 x 2000 mm |
PREPARED FOR INTEGRATION INTO PRODUCTION CELLS
The forming processes can be completed stepwise in transfer system to achieve very short cycle times. Simultaneous axis movements ensure fast production processes and an efficient and highly dynamic production.
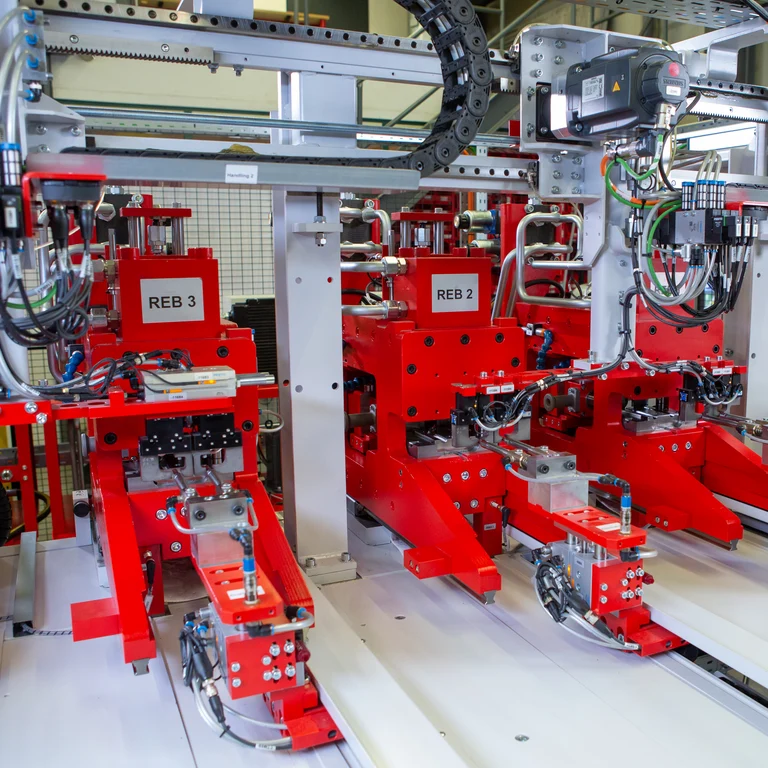
EASY CONTROL VIA TOUCH PANEL
Setting of all parameters centrally in the machine control system, controlled positioning of the forming axis and the stop position.
The SRM is equipped with a completely electronic preselection of the flanging geometry. The stop position and all strokes and machining operations are servo-electrically controlled and can be called up via a touch panel.
Decisive for the exact machining time is which material is used and which shaping is to be implemented. The machine carries out the processing quasi automatically if it is possible to call up the tube size with the necessary process parameters. In individual cases, the clamping lengths for machining are 1 to 1.5 x the pipe diameter.
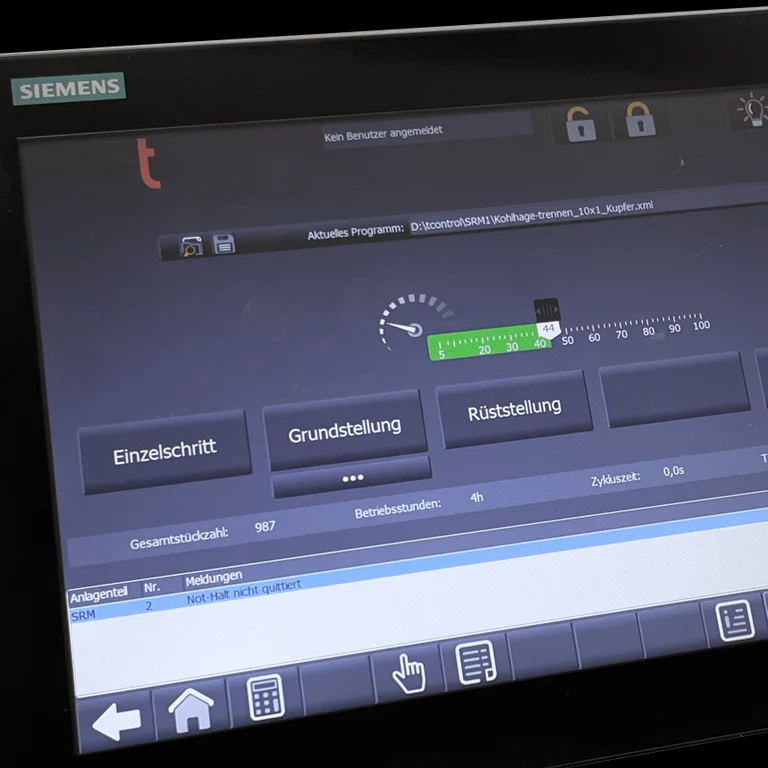
The solution for any geometry with outstanding sealing surfaces
Tailored to your individual requirements and needs, we create optimal solutions with our expertise.
Production samples
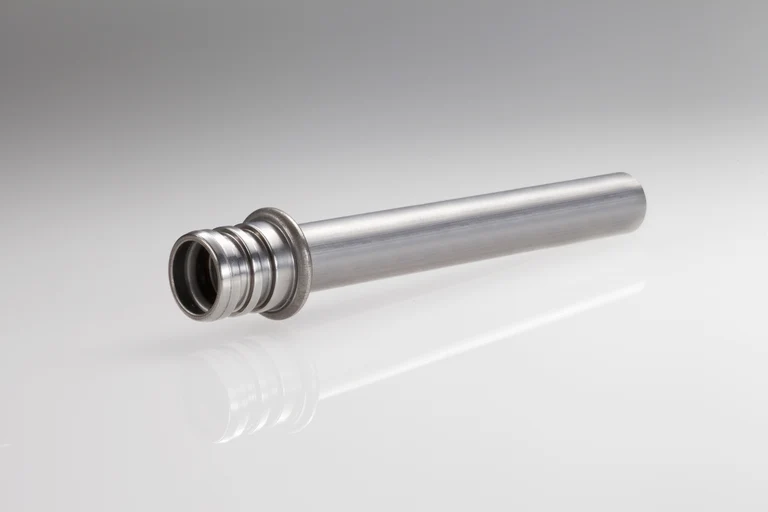
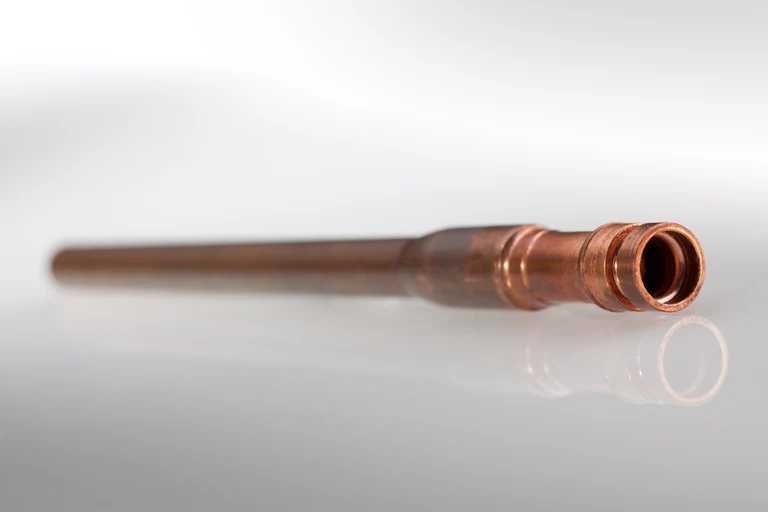
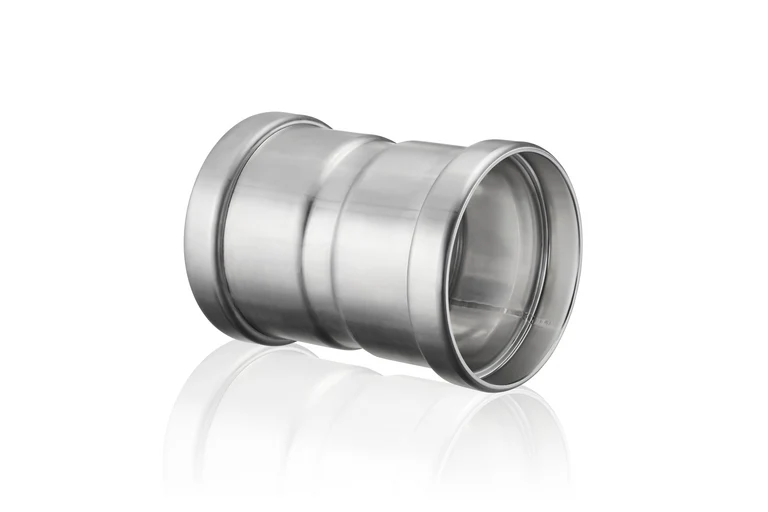
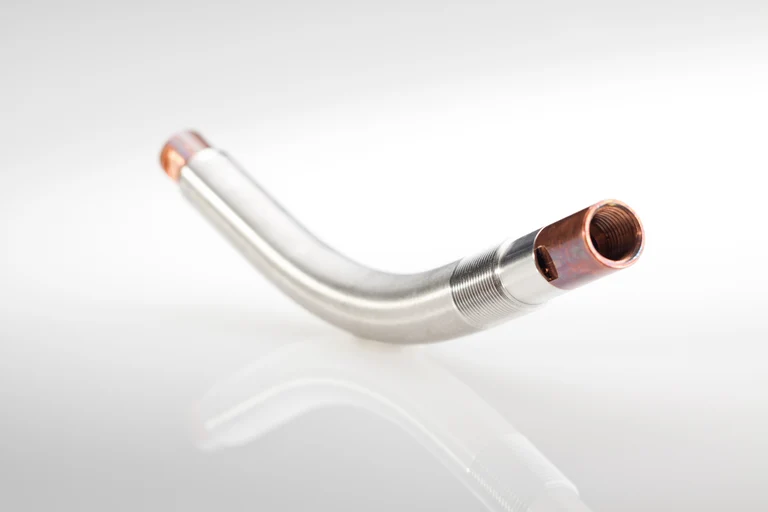
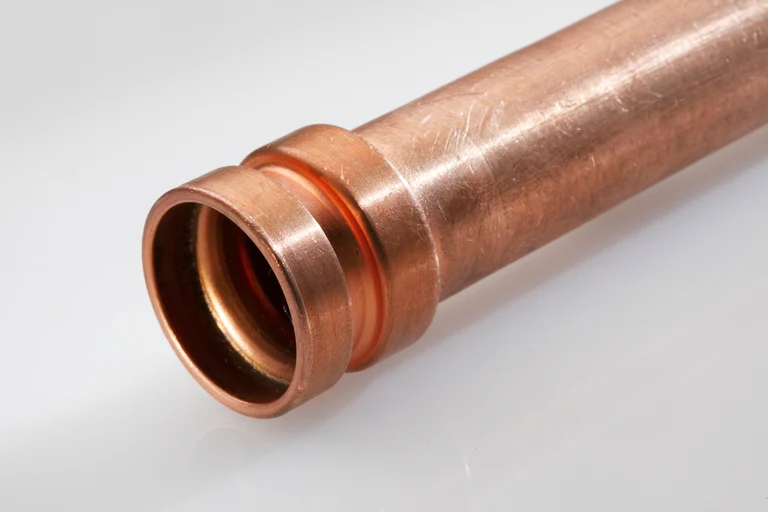
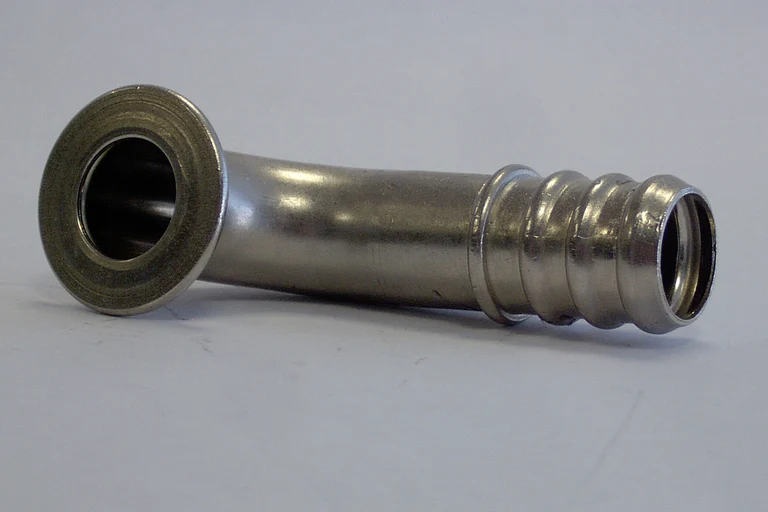
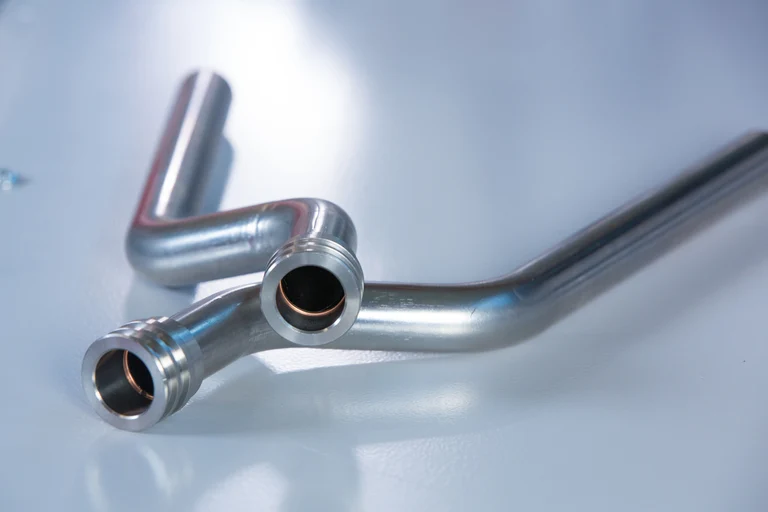
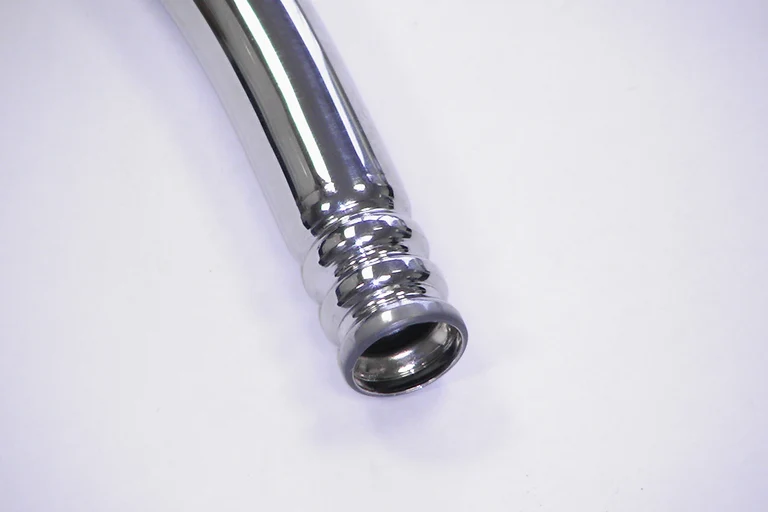
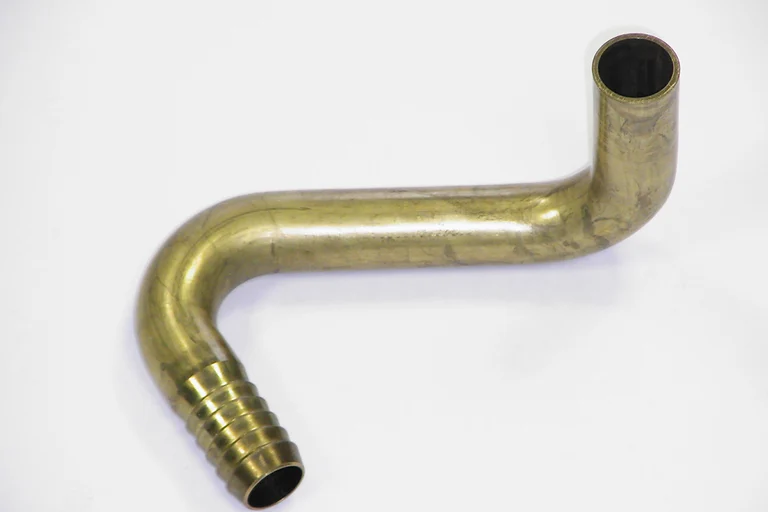
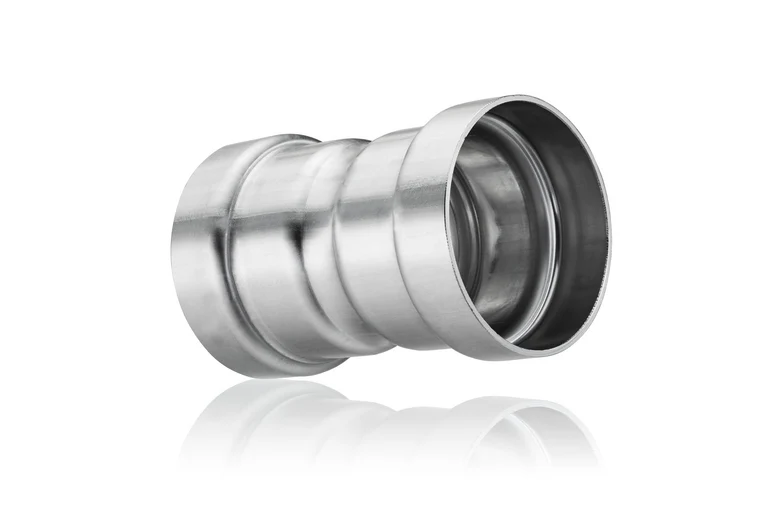
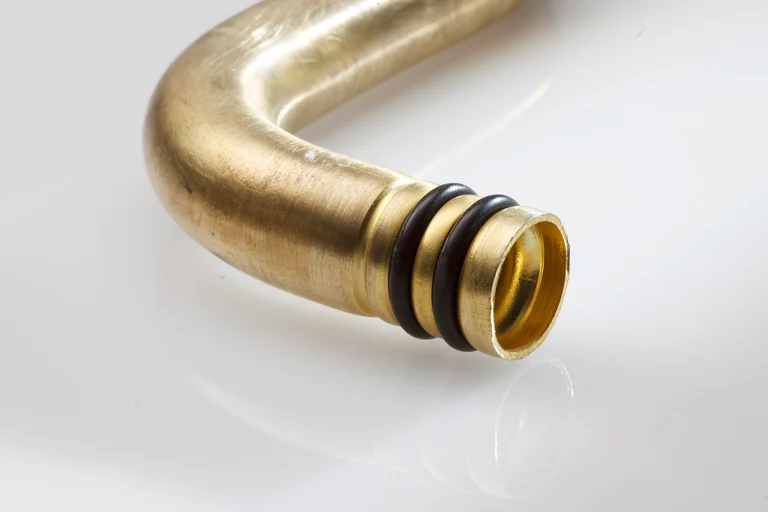
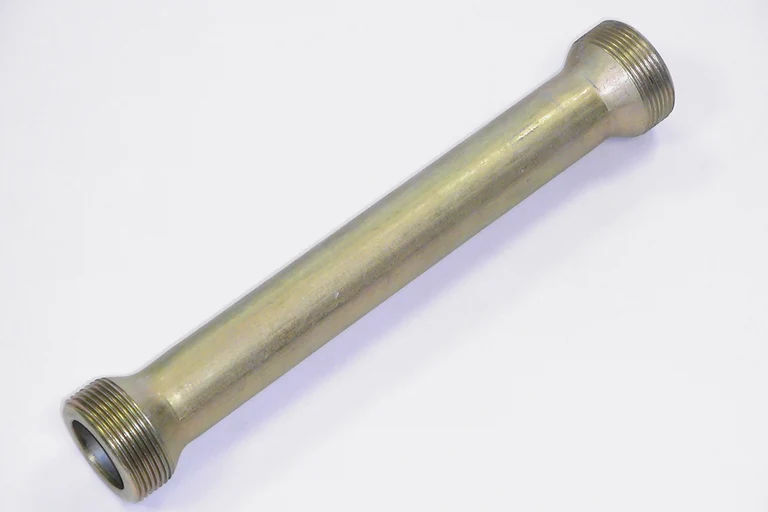
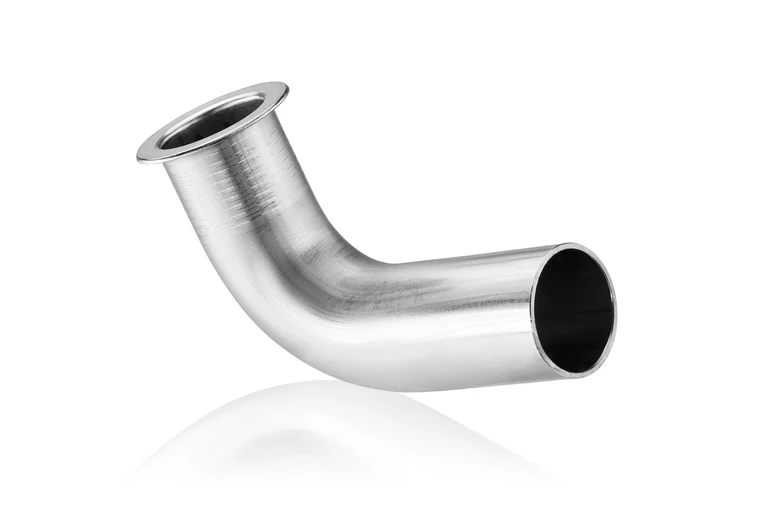
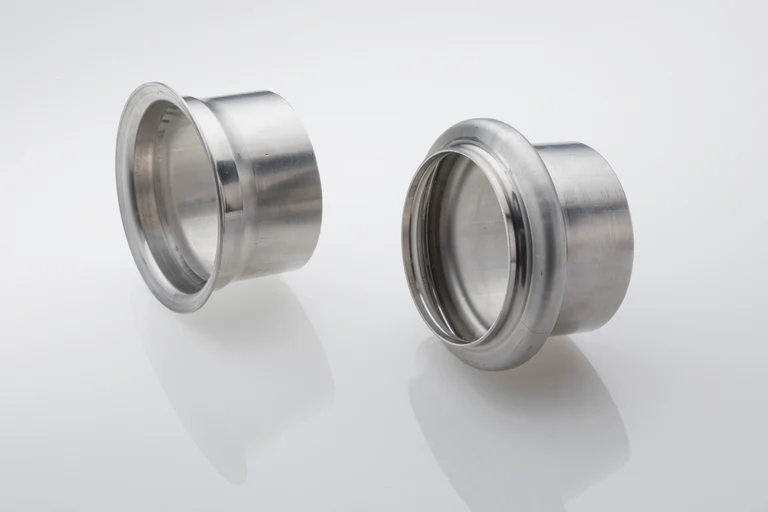
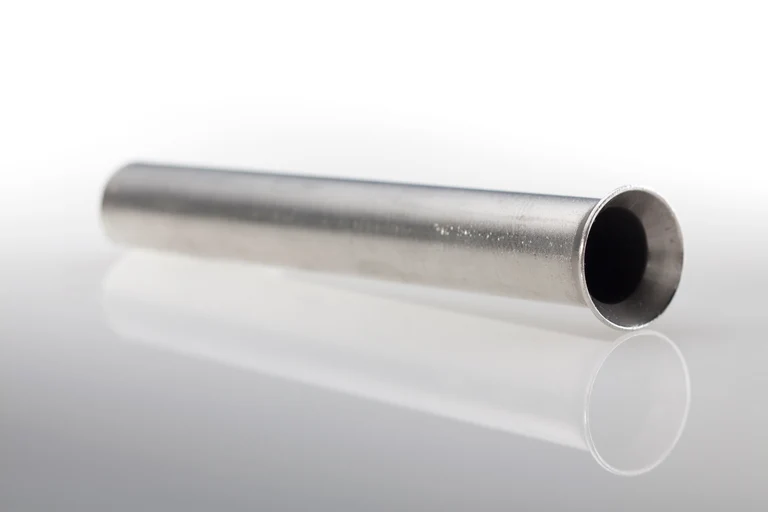
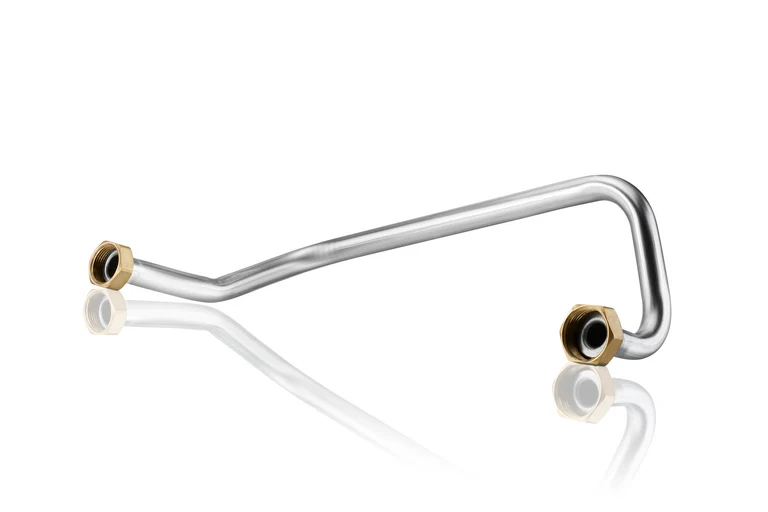
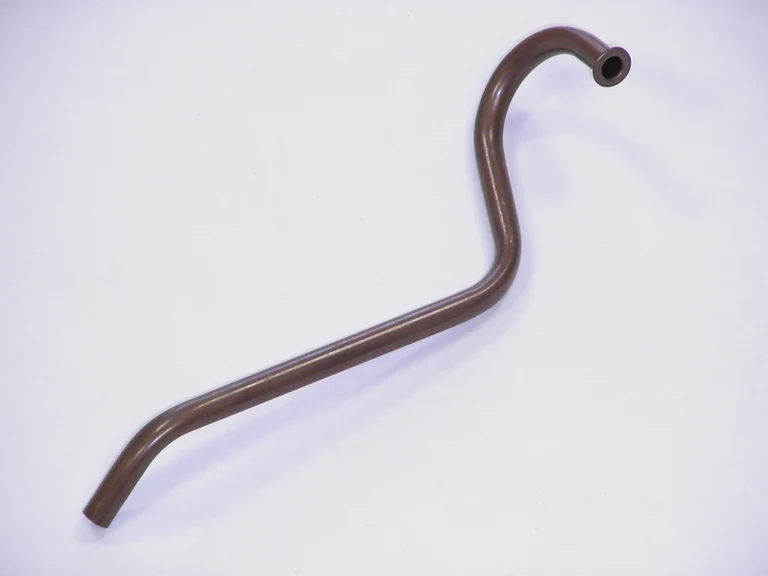
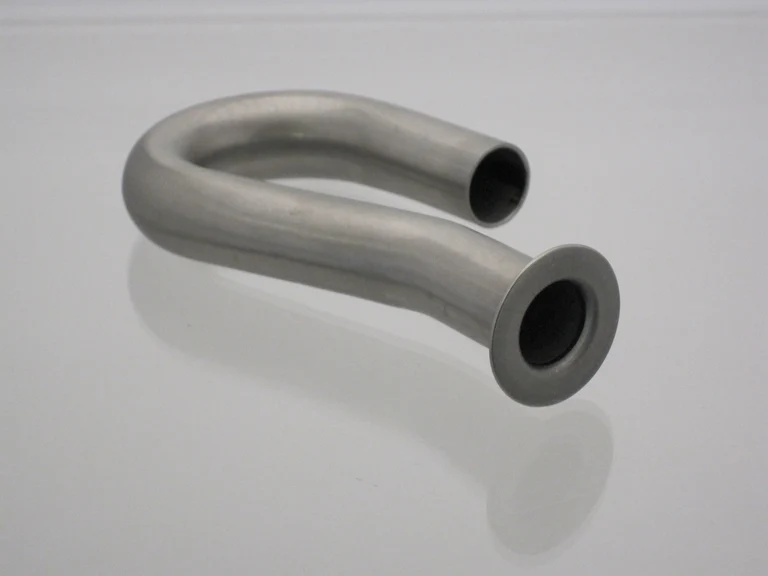
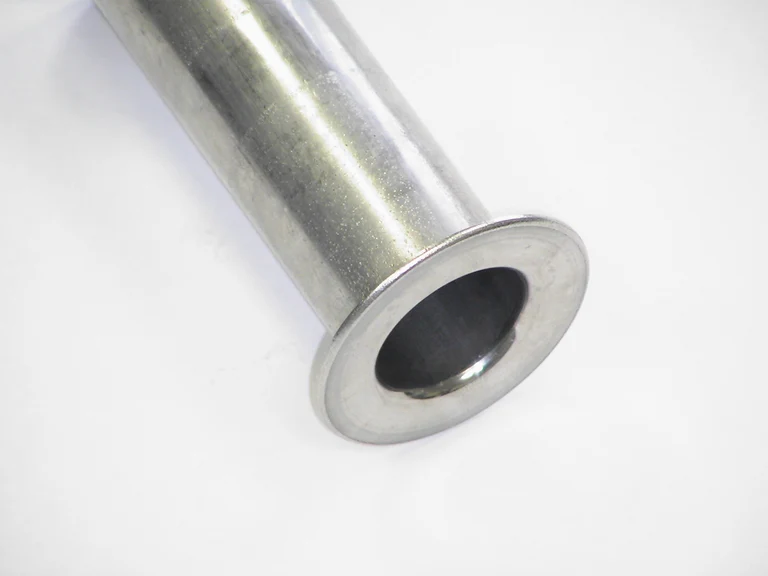
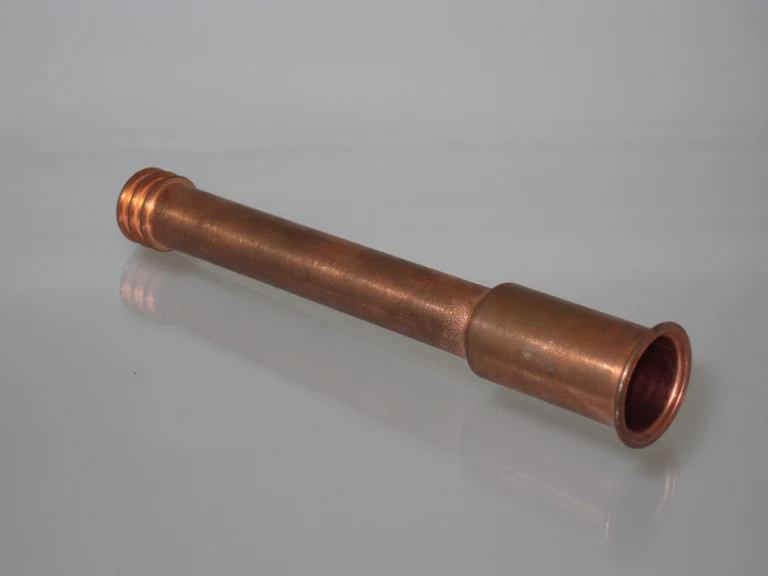
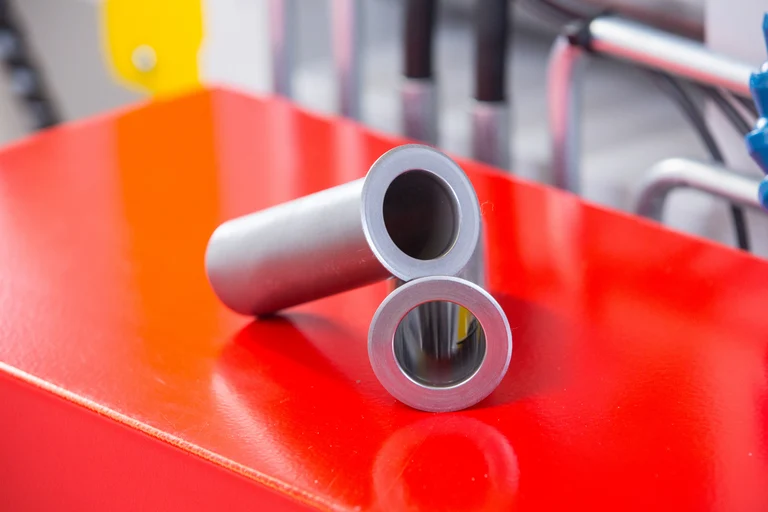
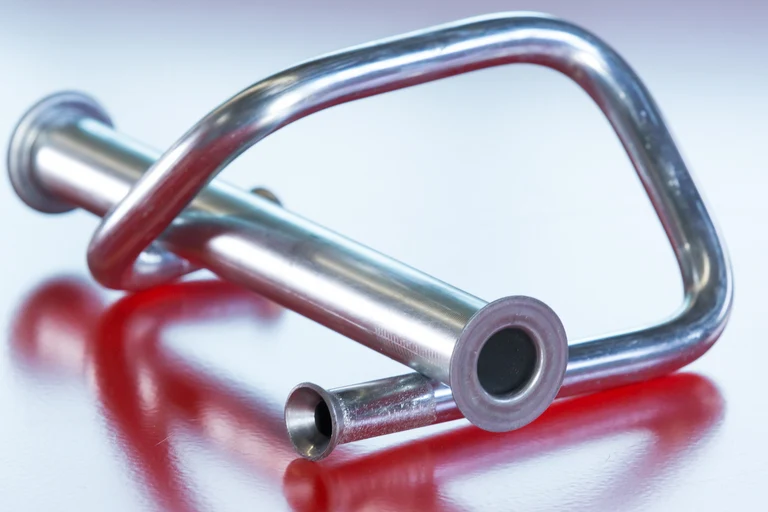
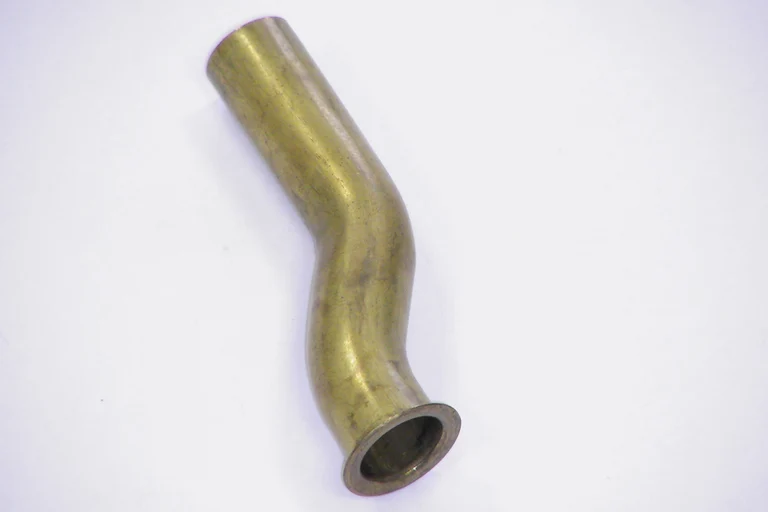
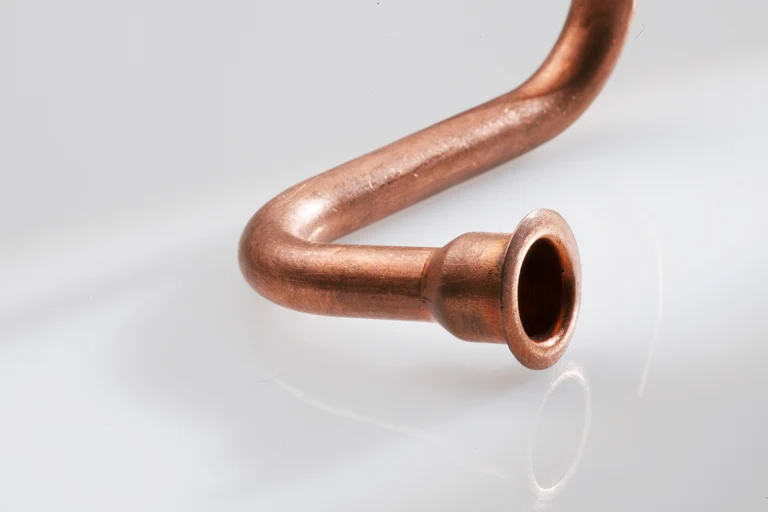
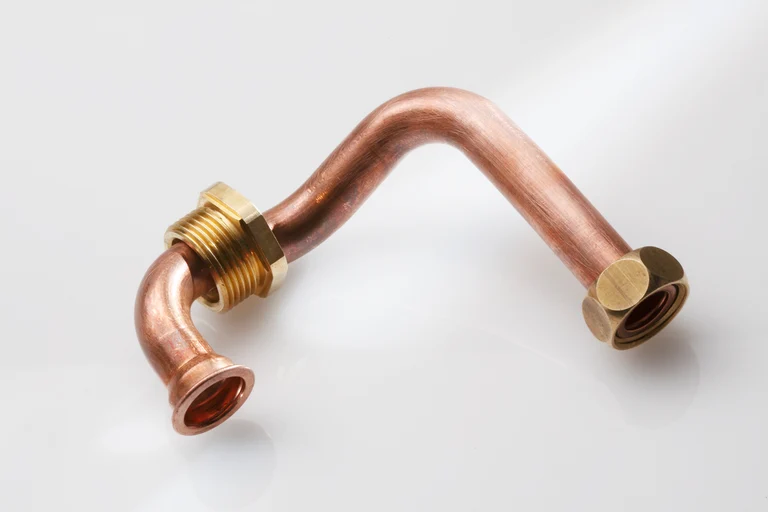
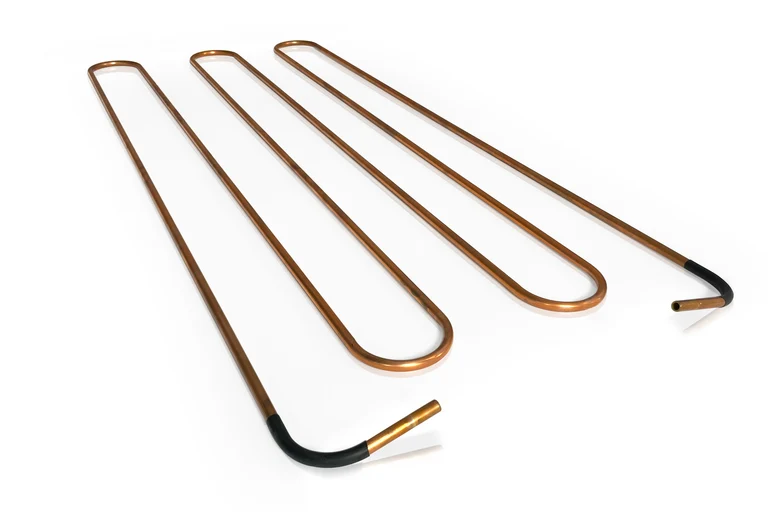
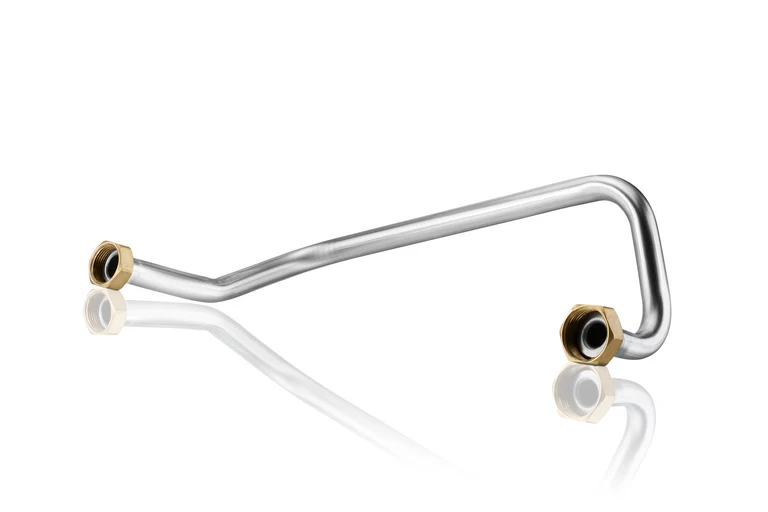
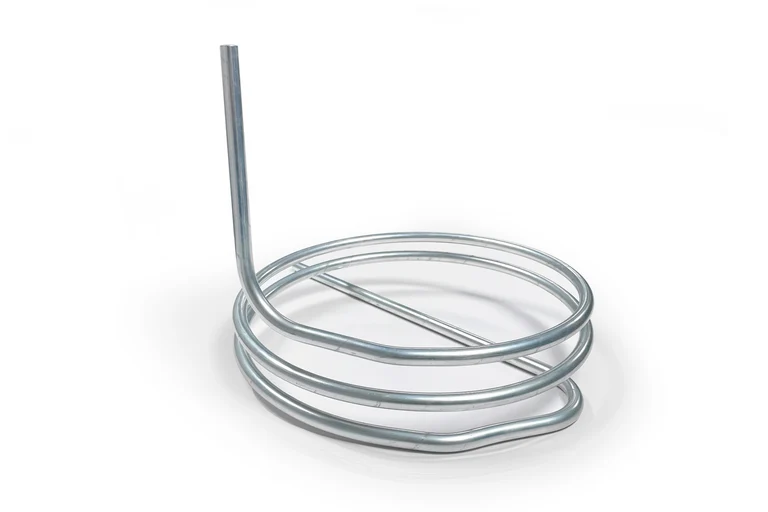
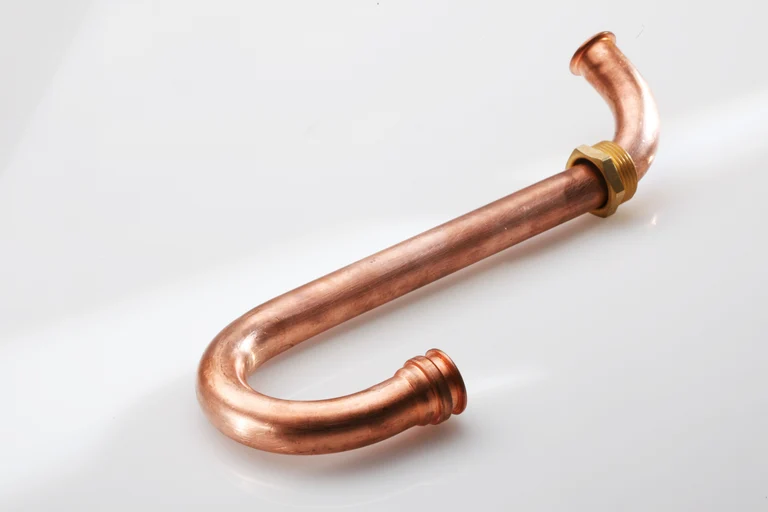
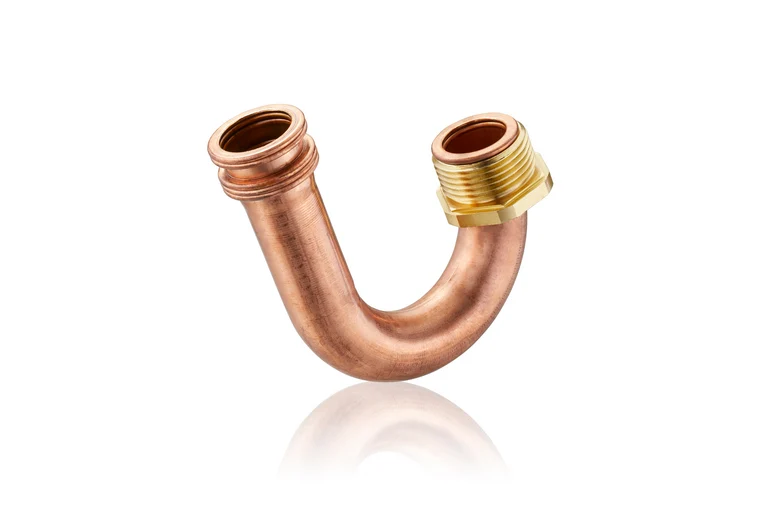
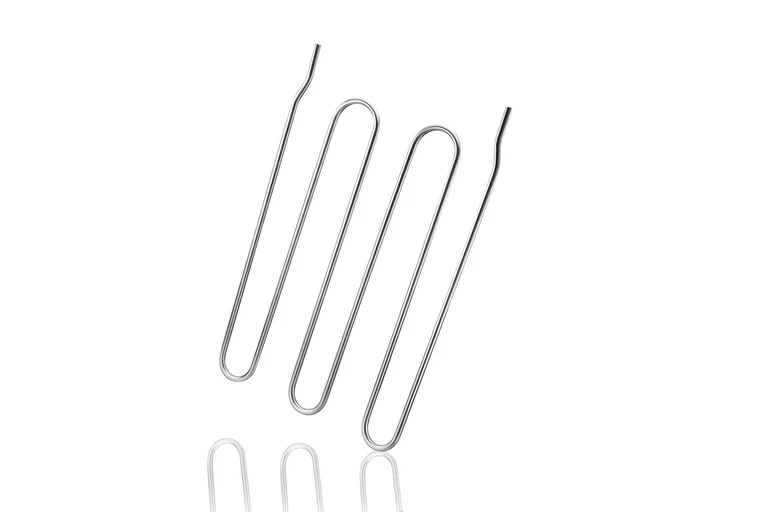
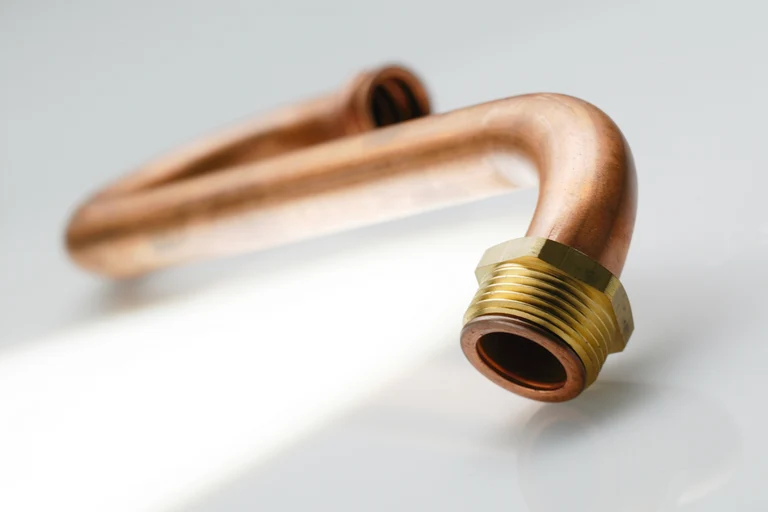
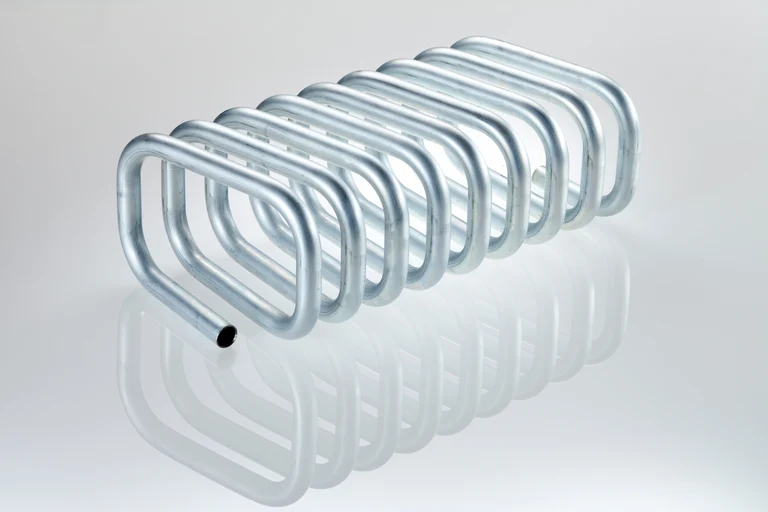
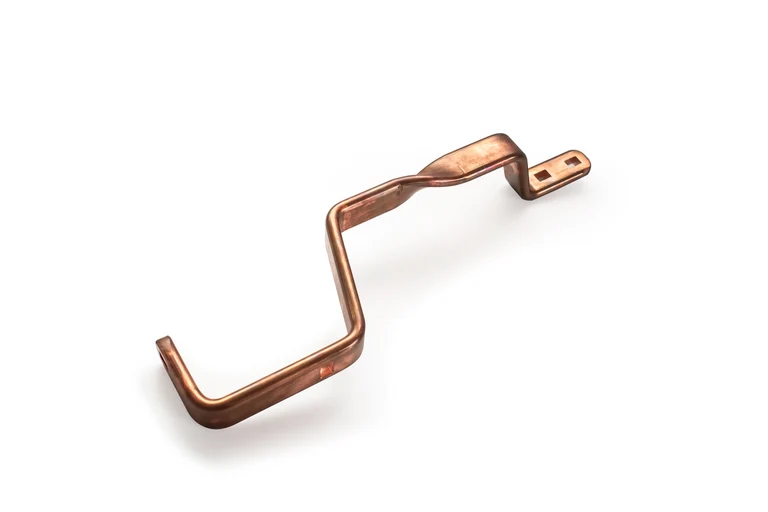
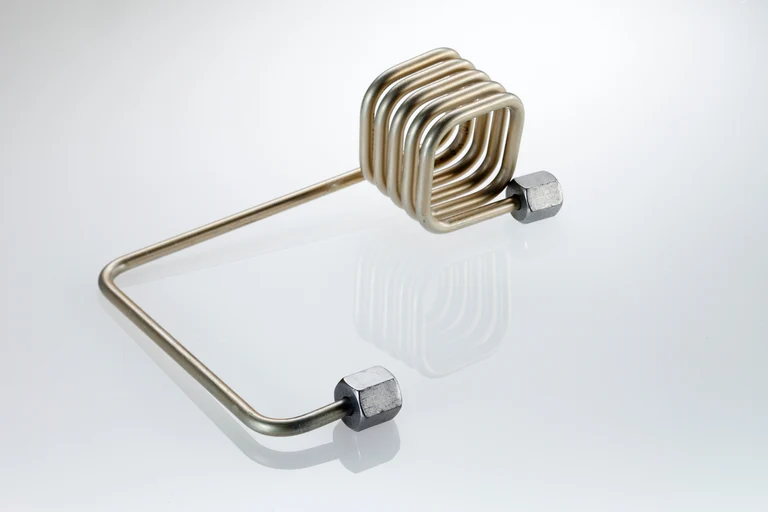
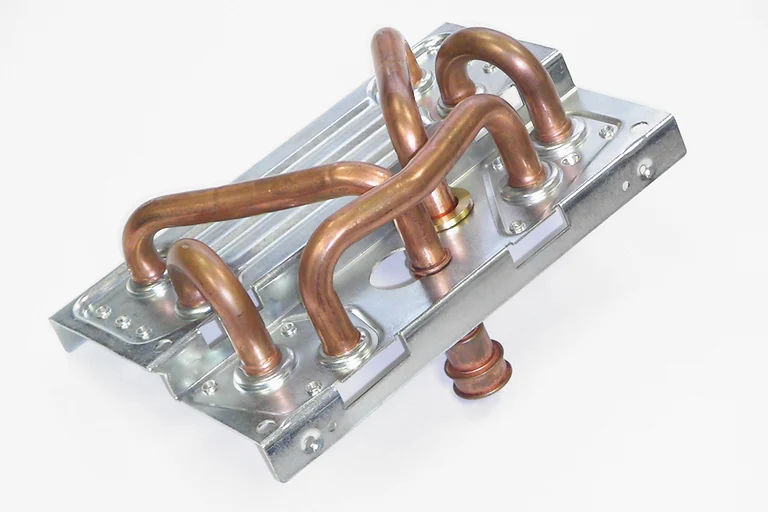
Catalog Download
transfluid® offers the complete package for the production of tubing.
Download our new catalogue.
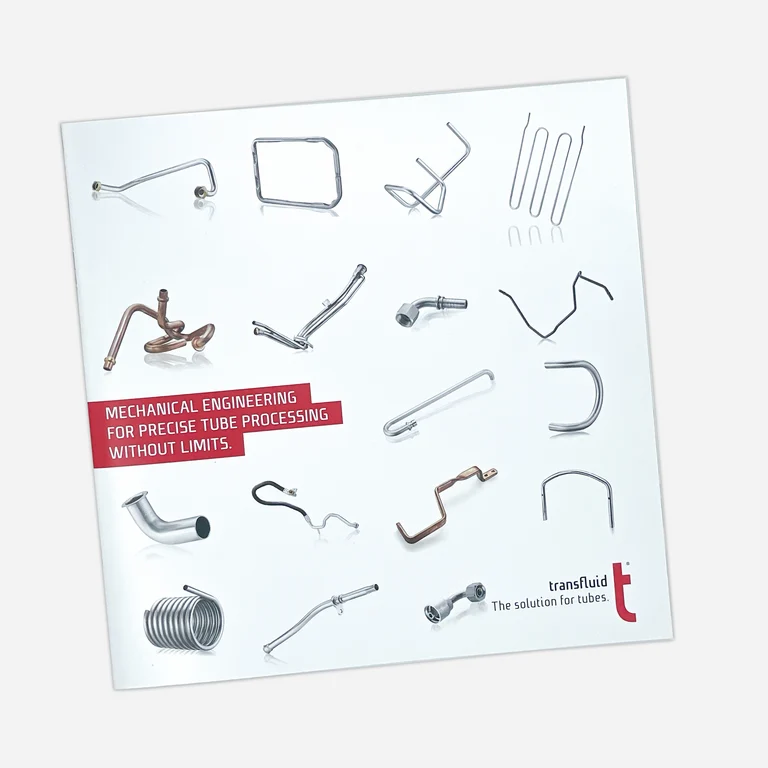