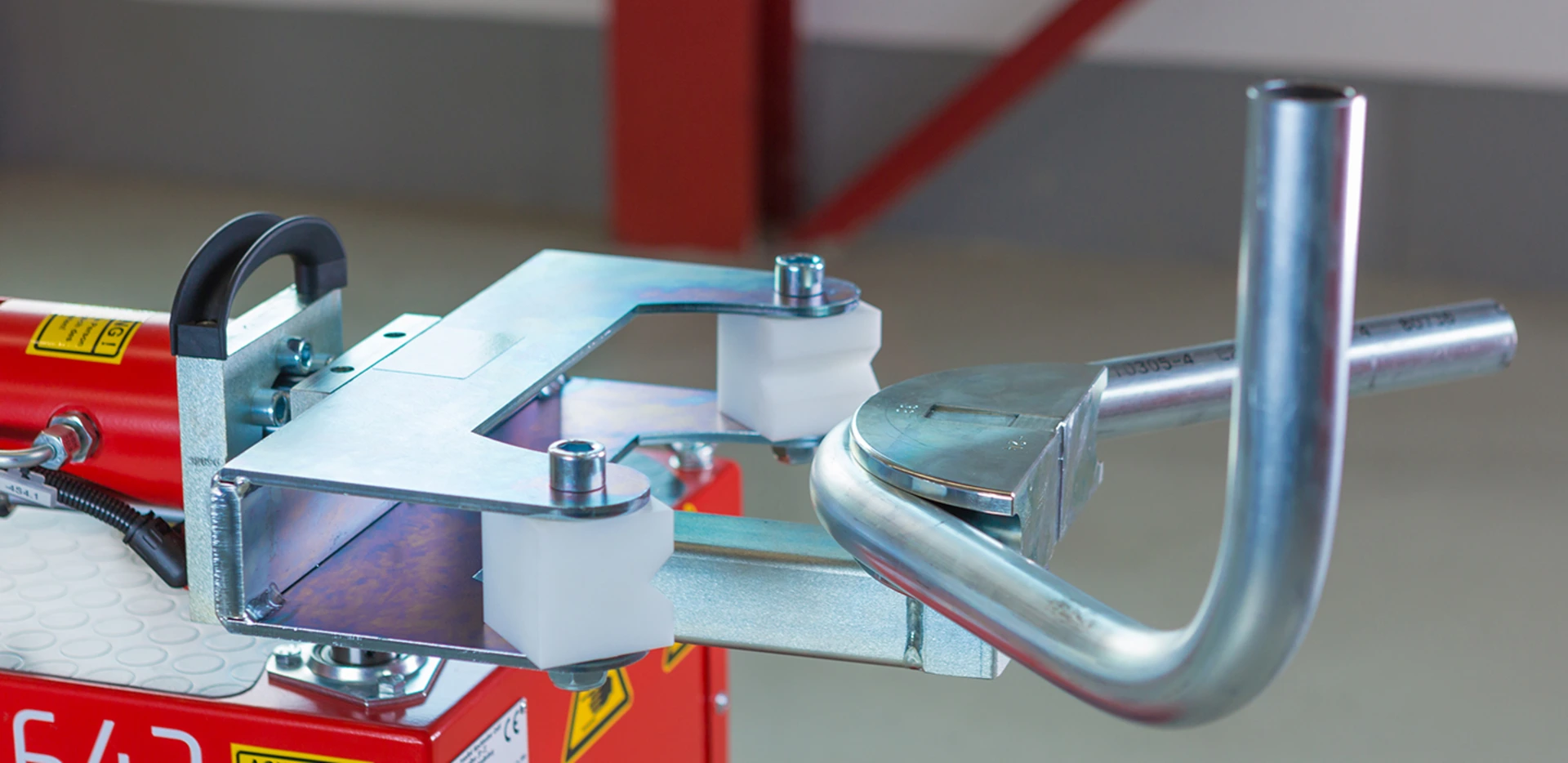
MOBILE AND COMPACT t work TUBE BENDING MACHINES
THE SMART SOLUTION FOR BENDING TUBES.
Performance made to measure!
Machines to shape tubes anywhere and in small series. We can deliver the ideal tube bending machine for your application. Ourcompact and mobile tube bending machines are movable on casters and can be used on site during the installation. The mobile use gives improved flexibility for individual bending tasks. With our stationary mandrel bending machine you will have complete freedom to bend small and medium sized runs of tubes. The practical optional functions, such as pre-assembly, flaring, deburring and cutting, make the full processing of tubes possible.
Catalog Download
transfluid® offers the complete package for the production of tubing.
Download our new catalogue.
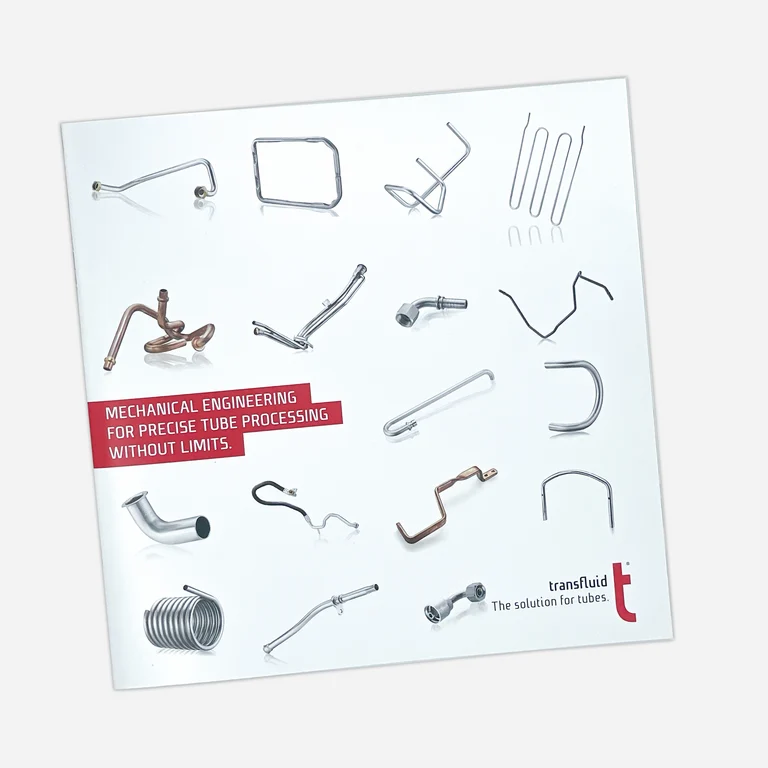