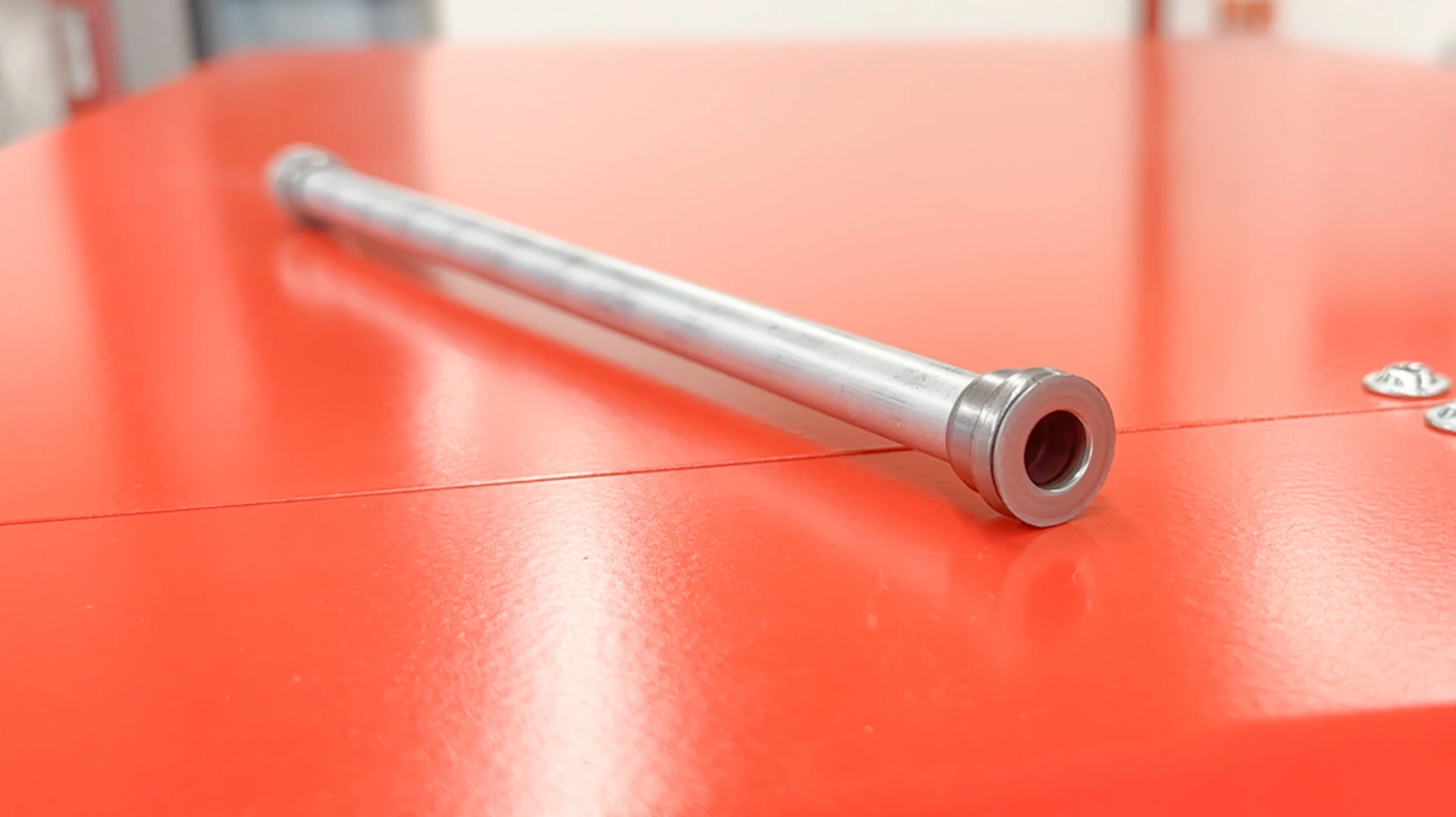
INCORRECT ASSEMBLY IMPOSSIBLE!
ORFS CONNECTIONS MANUFACTURED SEMI-AUTOMATICALLY
Faster pipe end forming and better surfaces
t form UMR forming machine from transfluid with easy tool change and minimized operator input
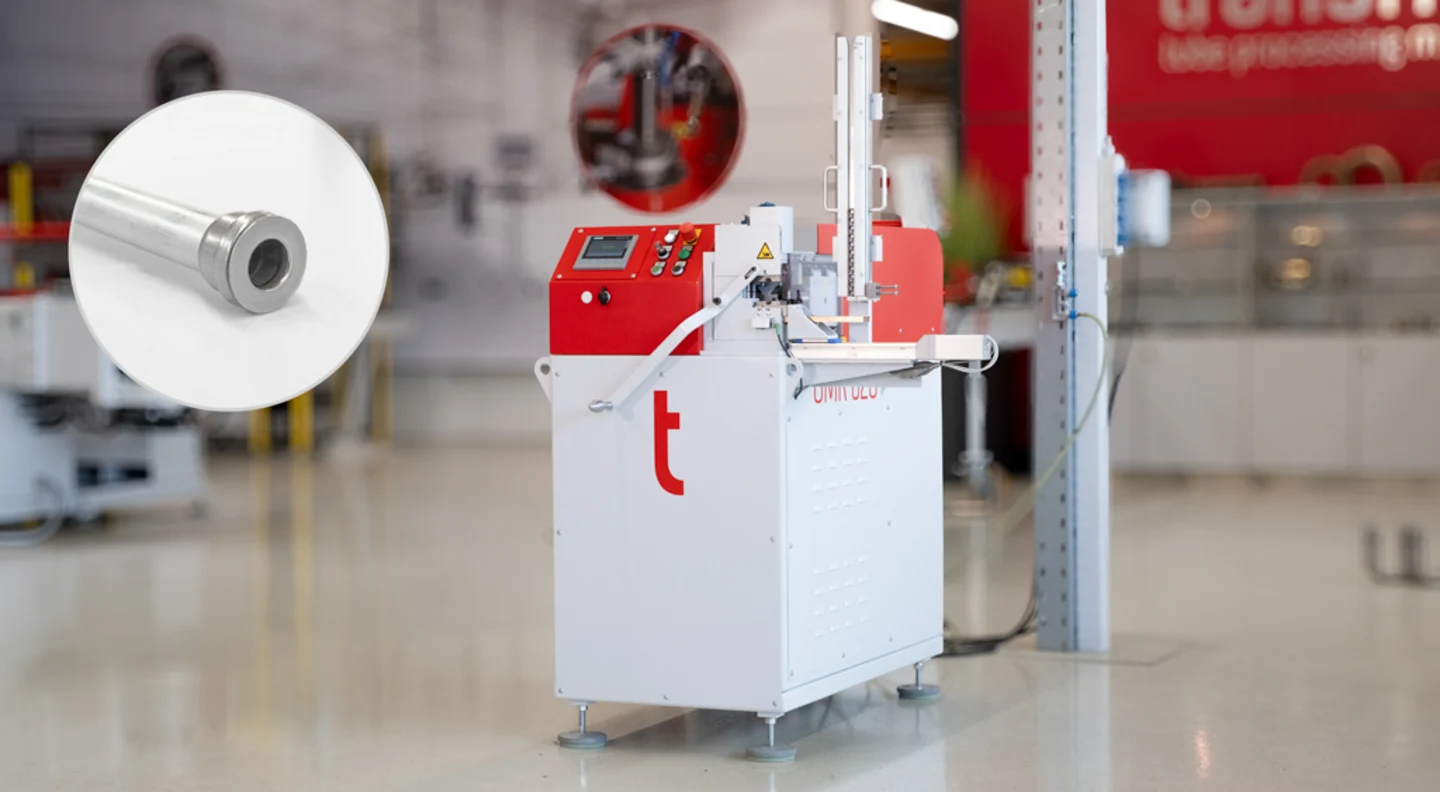
EASY CONTROL VIA TOUCH PANEL
Setting of all parameters centrally in the machine control system, controlled positioning of the forming axis and the stop position.
The UMR is equipped with a completely electronic preselection of the flanging geometry. The stop position and all strokes and machining operations are servo-electrically controlled and can be called up via a touch panel.
Decisive for the exact machining time is which material is used and which shaping is to be implemented. The machine carries out the processing quasi automatically if it is possible to call up the tube size with the necessary process parameters. In individual cases, the clamping lengths for machining are 1 to 1.5 x the pipe diameter.
Our new generation of t form UMR 628, 642 and 30115 machines reduces the set-up time when changing the tools and the operator can set up the machine in less than three minutes.
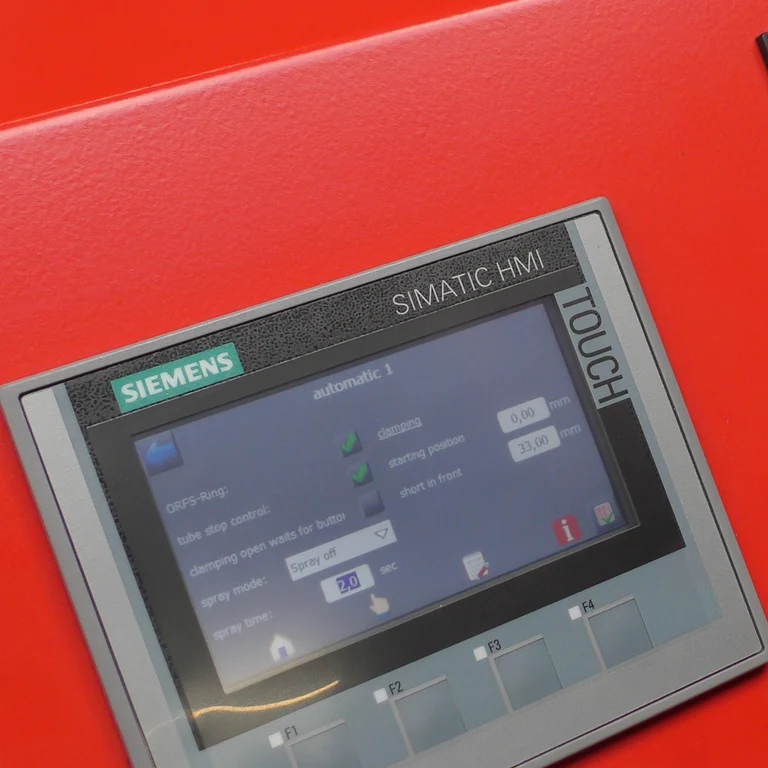
The solution for any geometry with outstanding sealing surfaces
Tailored to your individual requirements and needs, we create optimal solutions with our expertise.
Production samples
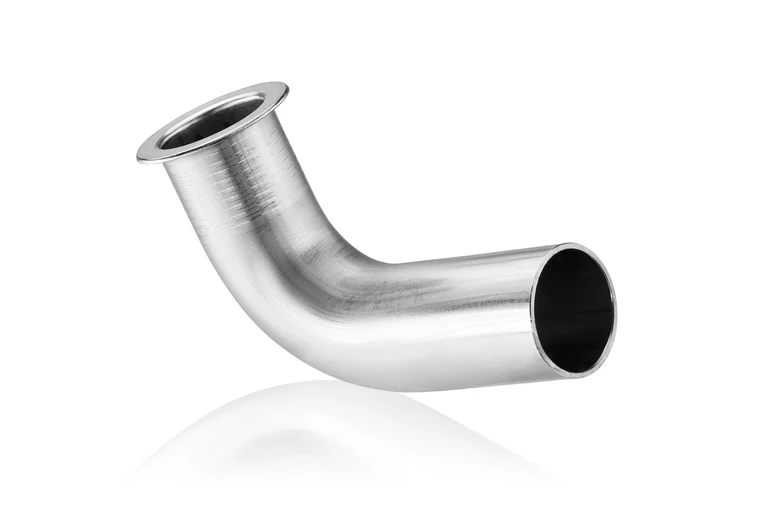
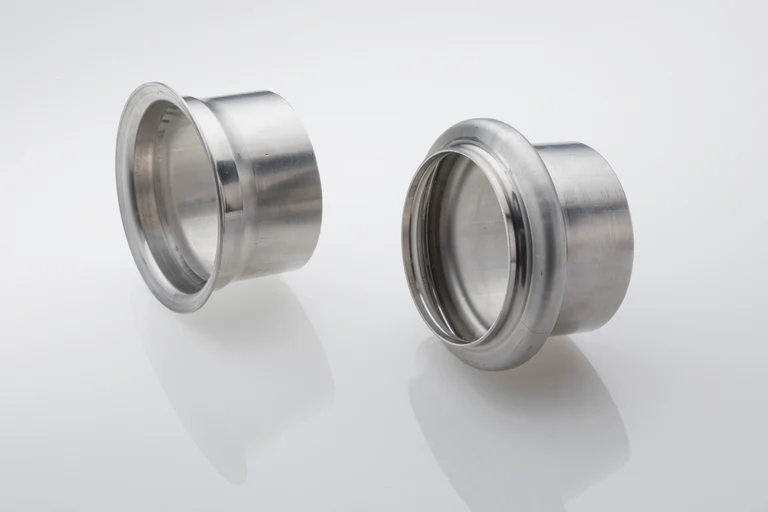
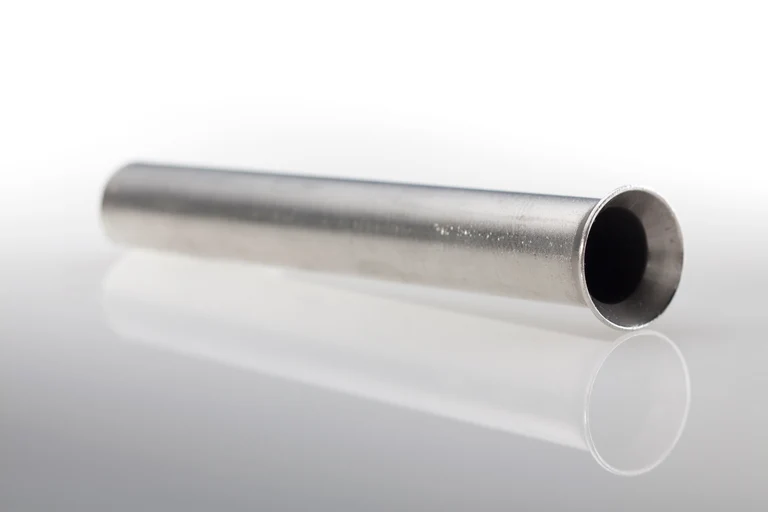
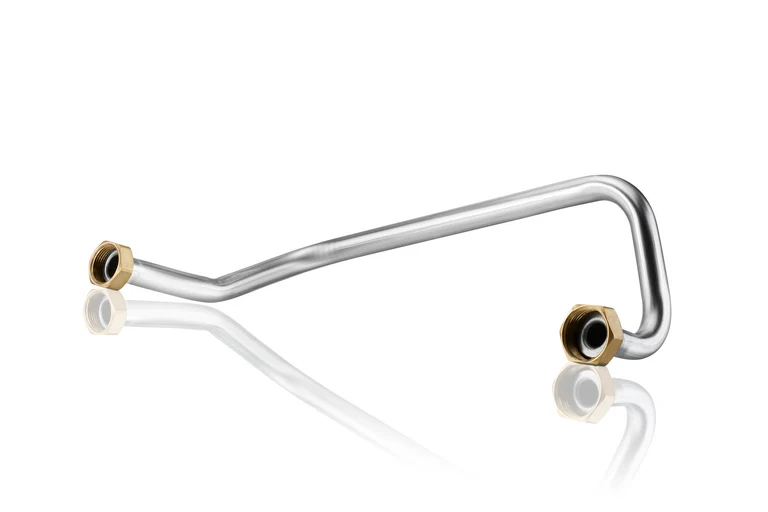
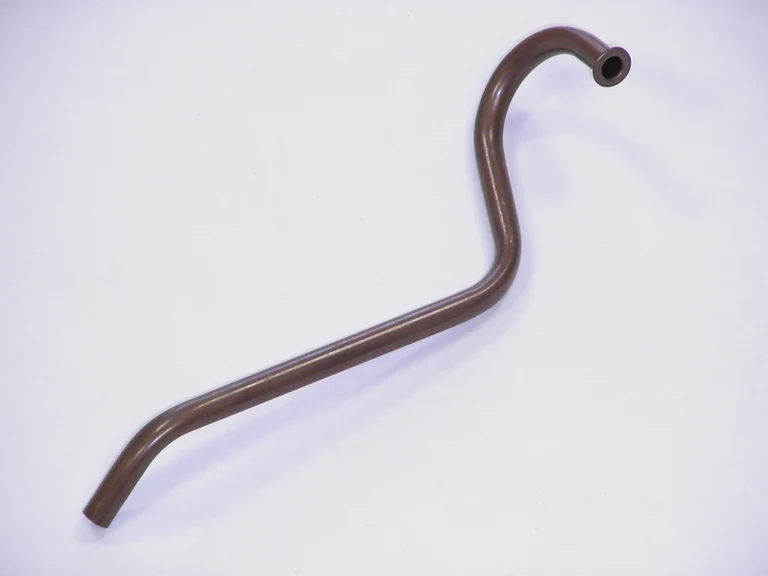
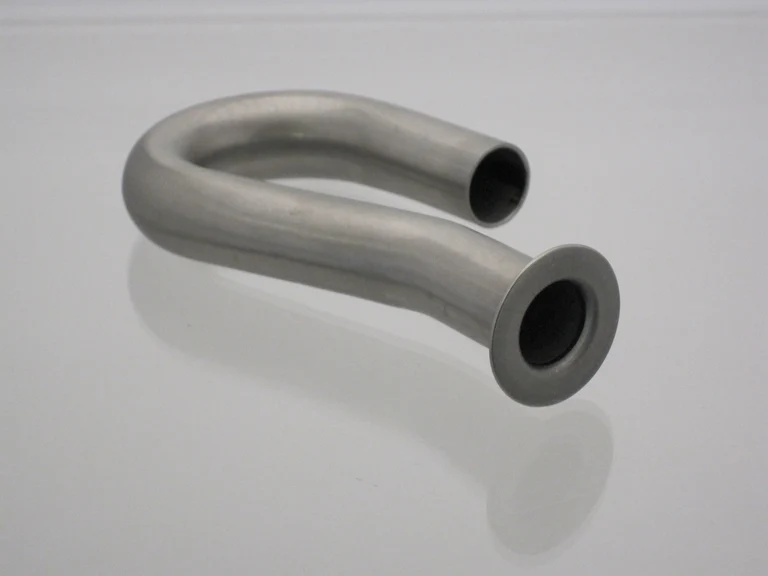
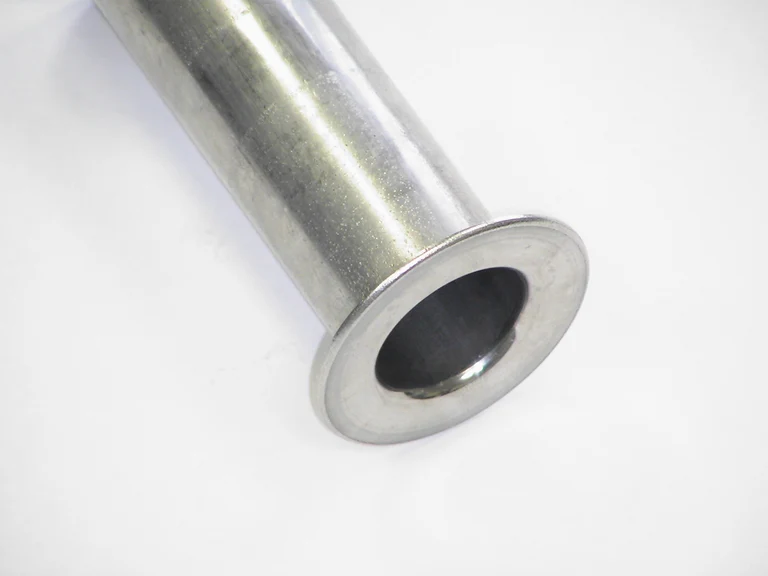
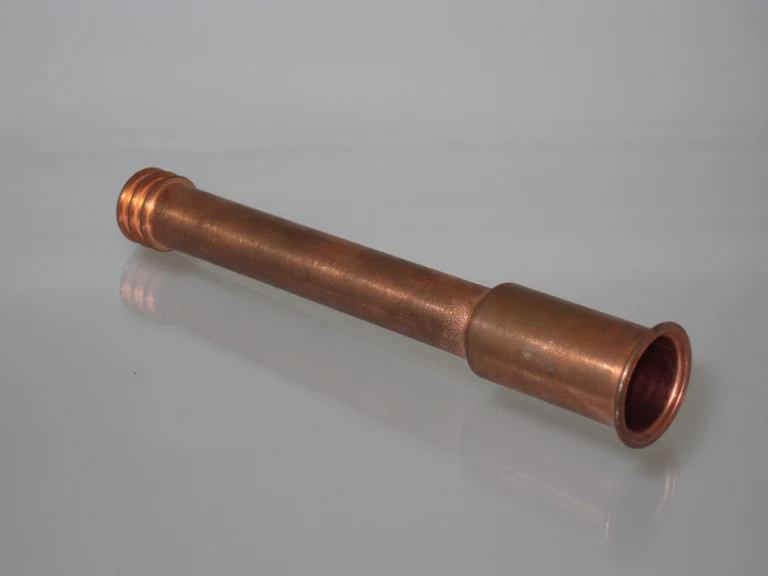
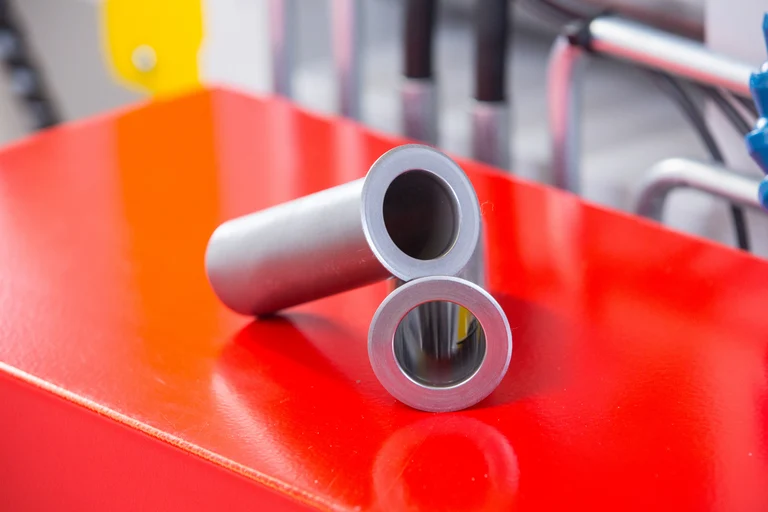
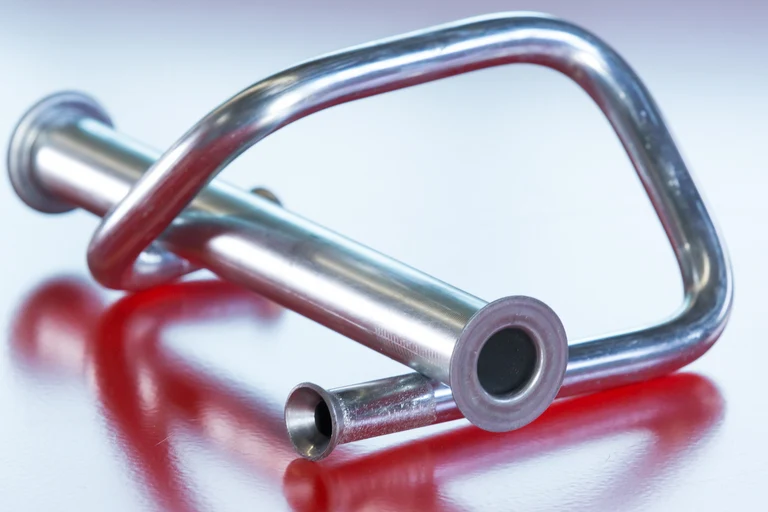
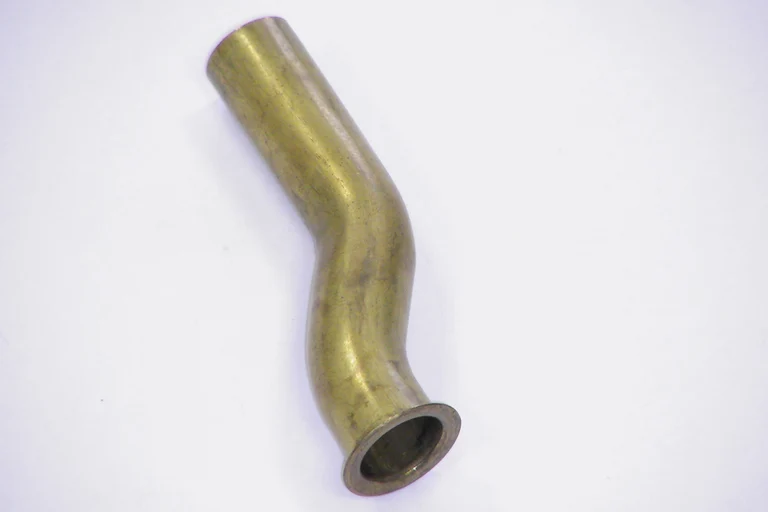
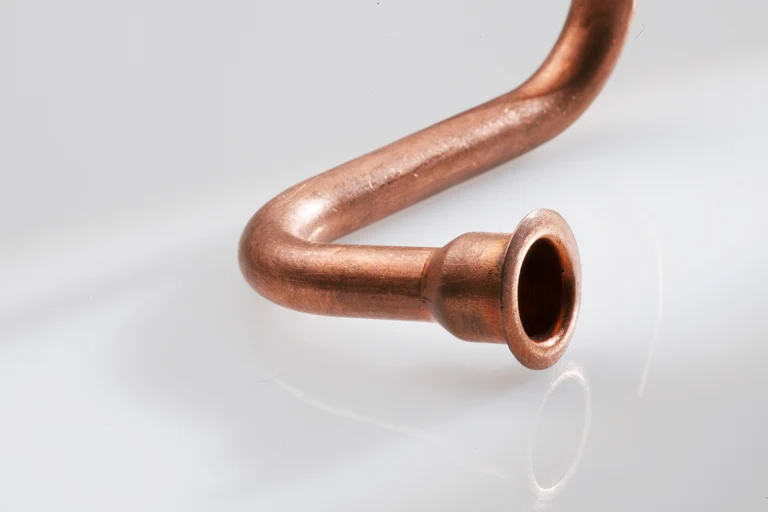
Catalog Download
transfluid® offers the complete package for the production of tubing.
Download our new catalogue.
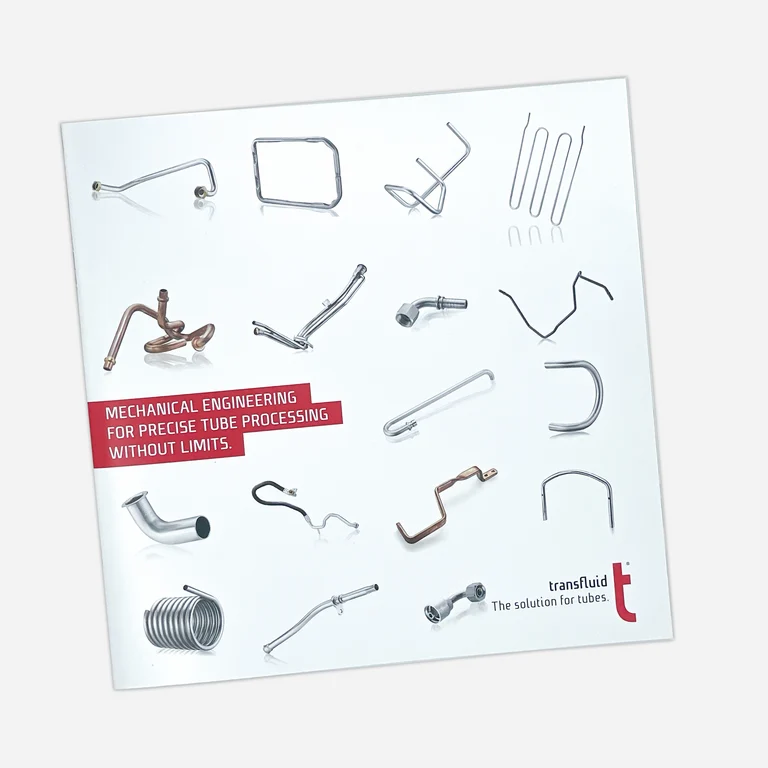