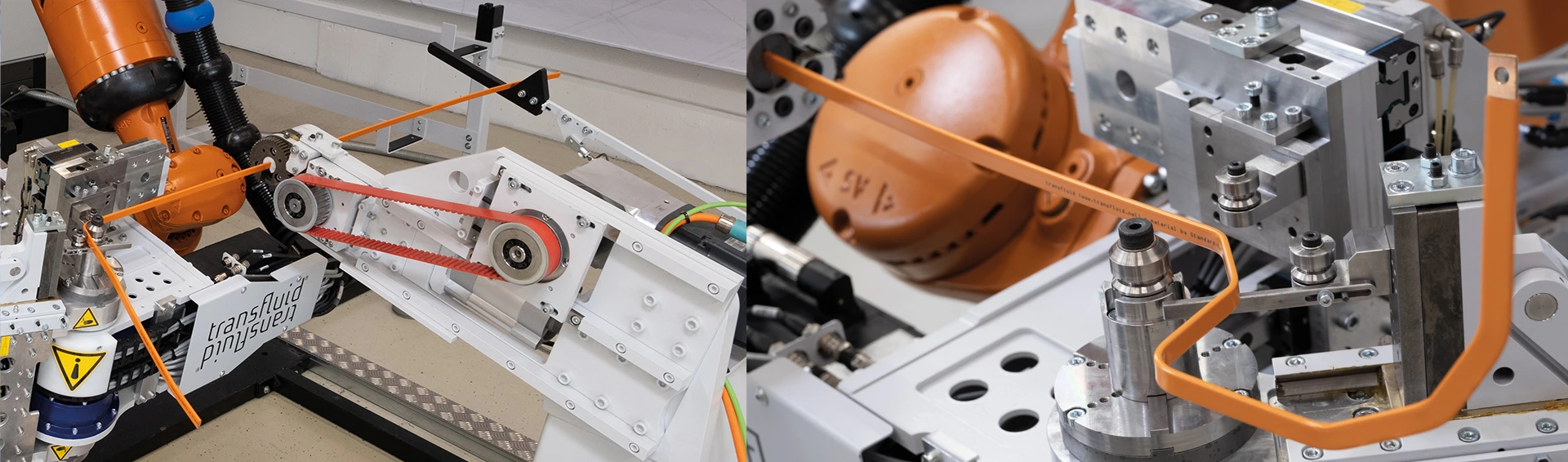
transfluid® ENERGY FLOW BROUGHT INTO SHAPE.
Extremely long busbars cut and bent automatically.
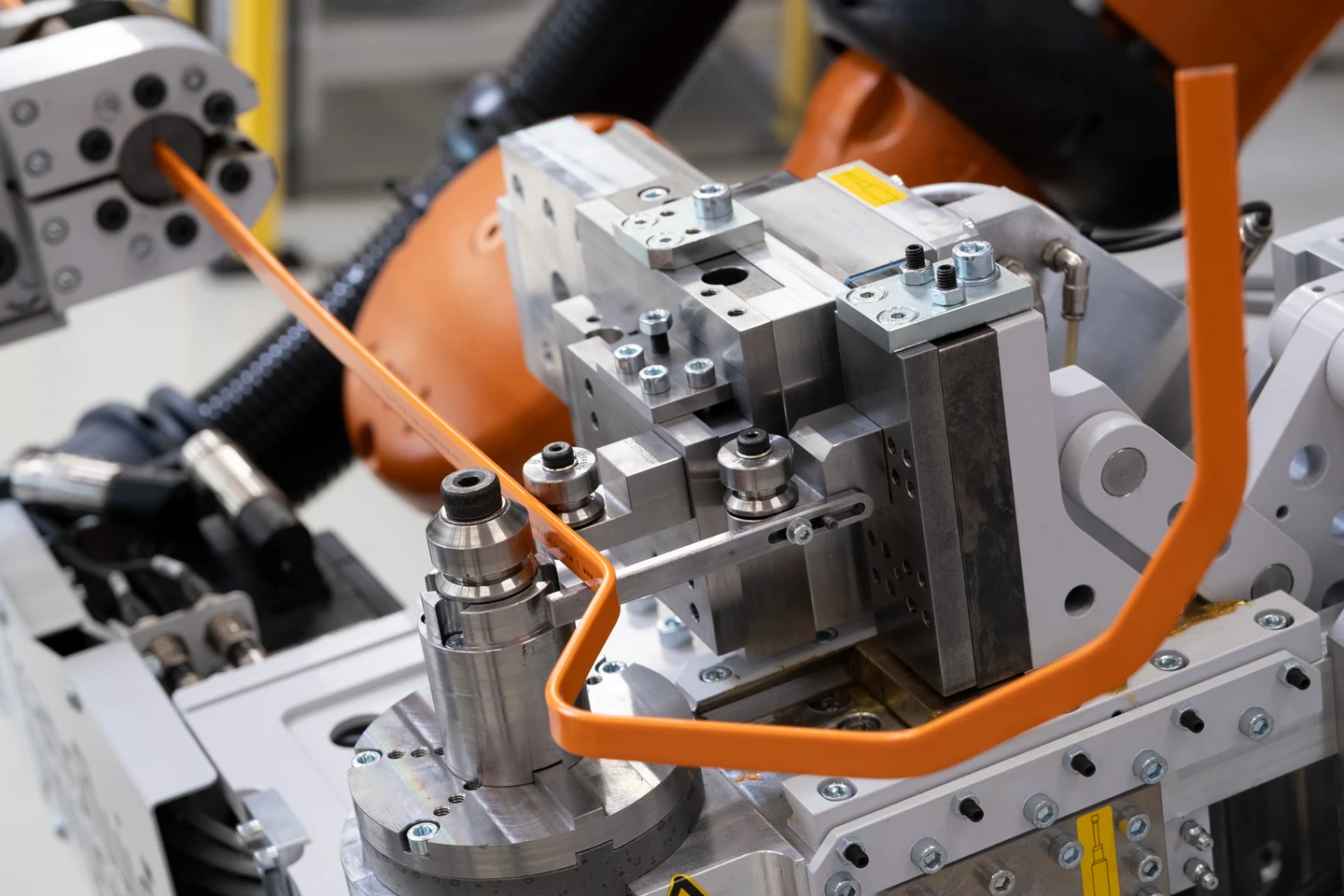
Open for third-party products.
The transfluid’s own software modules also make possible the integration of third-party products. This gives the customer the option of integrating and controlling measuring systems for quality assurance, as well as other additional processing units.
production samples
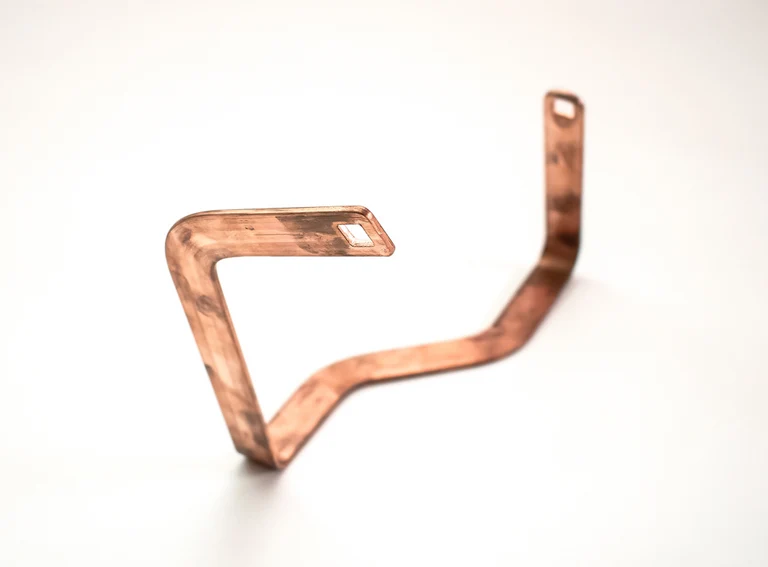
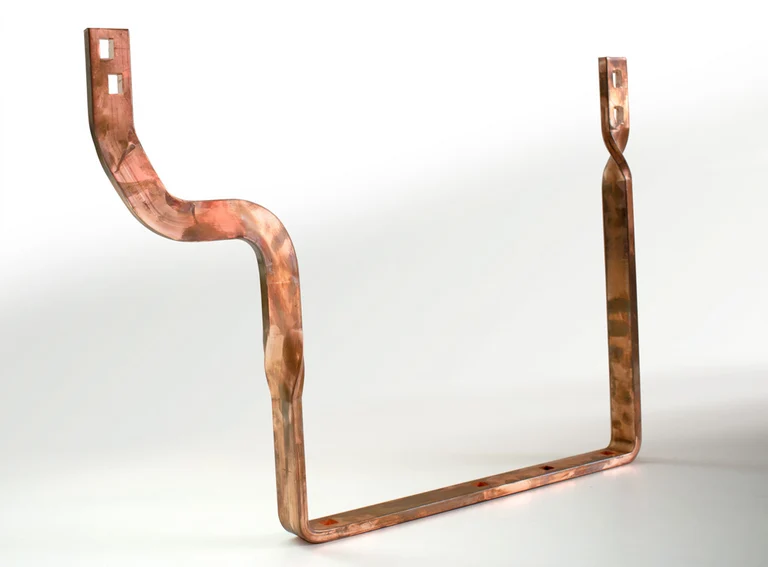
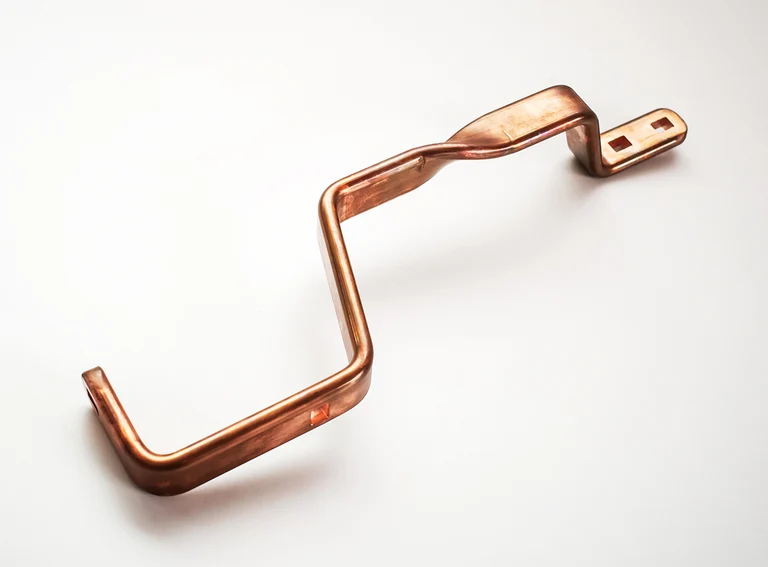
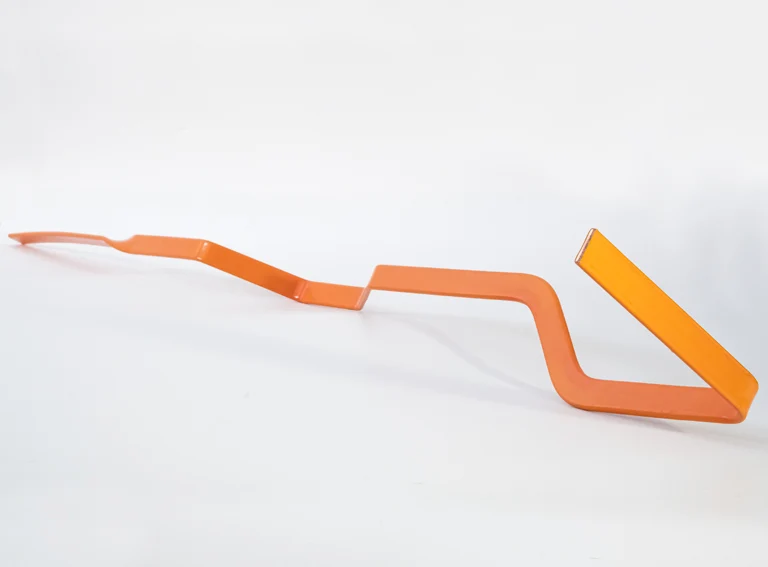
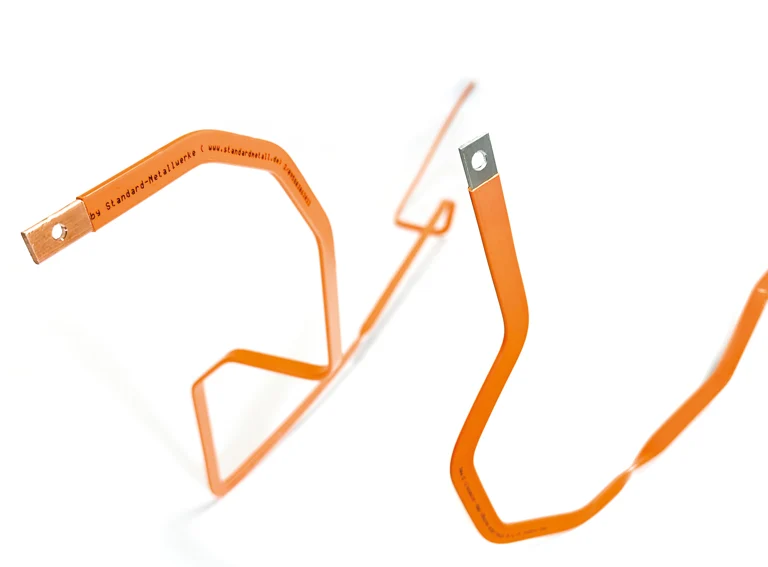
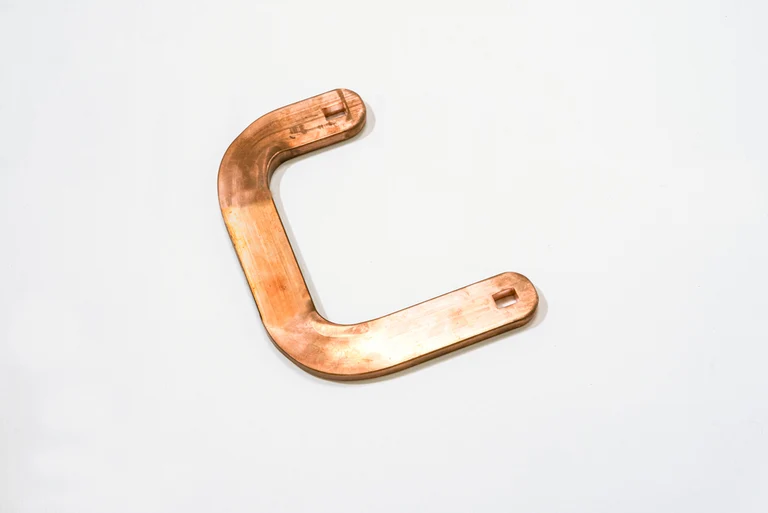
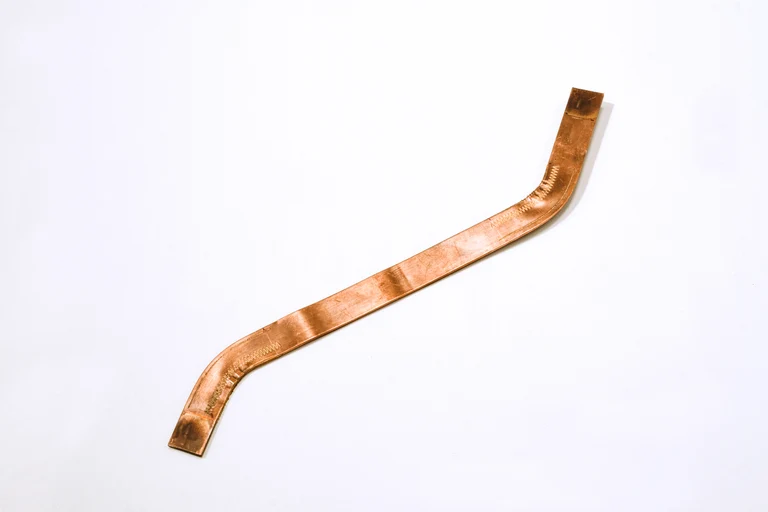
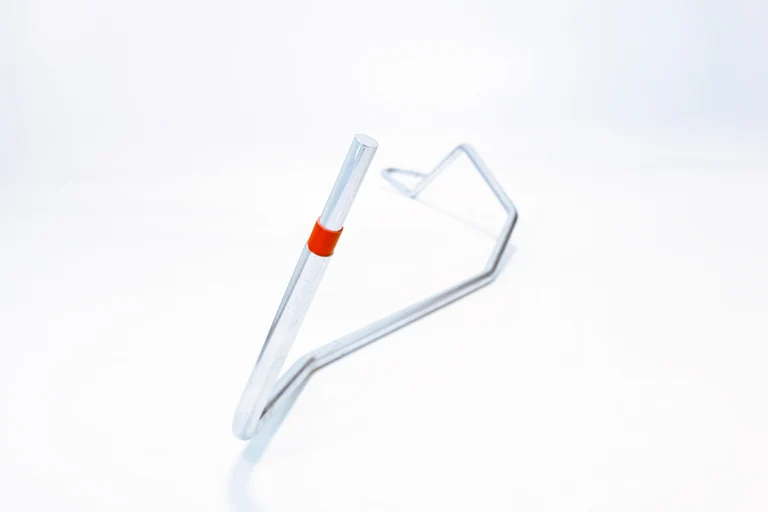
Not sure what you need?
We will find the right machine for your individual requirements. Our team of experts will be happy to advise you.
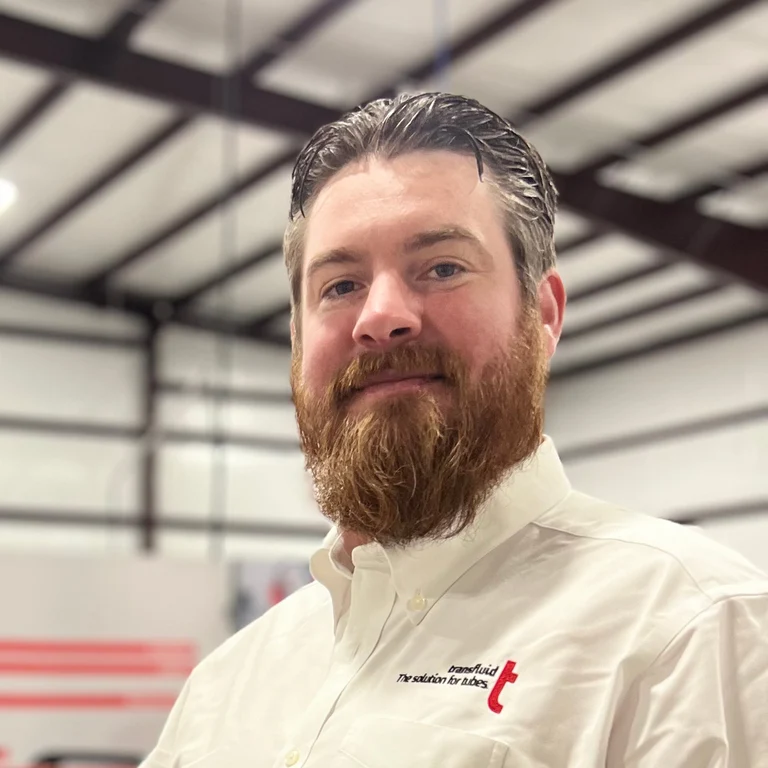